Stepped non-pillar continuous filling mining method for deep well super high large breaking ore body panel
A filling mining method and stepped technology, applied in special mining, filling, ground mining, etc., can solve the problems of small production capacity, low labor efficiency, and mutual interference in production, and achieve the effect of large production capacity and high mining intensity
- Summary
- Abstract
- Description
- Claims
- Application Information
AI Technical Summary
Problems solved by technology
Method used
Image
Examples
Embodiment 1
[0031] Shandong Gold Xincheng Gold Mine is one of the underground mines with the largest single gold output and the highest degree of mine mechanization in my country. It is mainly composed of I# and V# ore bodies, of which V# ore bodies are deep blind ore bodies, and the ore bodies are ellipsoidal It is located at the elevation of -430m~-732m, the length is 160m~180m, the thickness is 70m~120m, the dip angle of the ore body is 30°~40°, the average strike is NE40°, and it is inclined to the northwest. The ore grade is medium to high, with an average grade of 3.5g / t. The hanging wall of the ore body is the Jiaojia fault zone, which is very unstable, and the stability of the surrounding rock of the ore body and the foot wall is poor, and the F coefficient is 6-8. The V# ore body of Xincheng Gold Mine adopts the continuous filling mining method of panel stepped seamless column.
[0032] For specific implementation, see figure 1 , figure 2 , image 3 , Figure 4 with Figure...
PUM
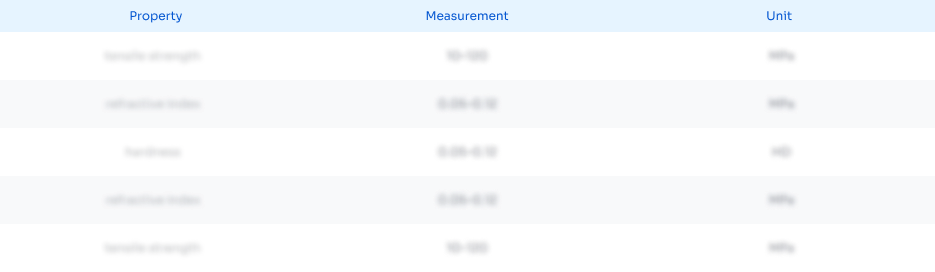
Abstract
Description
Claims
Application Information

- Generate Ideas
- Intellectual Property
- Life Sciences
- Materials
- Tech Scout
- Unparalleled Data Quality
- Higher Quality Content
- 60% Fewer Hallucinations
Browse by: Latest US Patents, China's latest patents, Technical Efficacy Thesaurus, Application Domain, Technology Topic, Popular Technical Reports.
© 2025 PatSnap. All rights reserved.Legal|Privacy policy|Modern Slavery Act Transparency Statement|Sitemap|About US| Contact US: help@patsnap.com