Calcium sulphate removal method of acid-leaching vanadium-extracted residues
A calcium sulfate and acid leaching technology, applied in the direction of improving process efficiency, can solve problems such as increased sulfur content, environmental pollution, and waste of resources
- Summary
- Abstract
- Description
- Claims
- Application Information
AI Technical Summary
Problems solved by technology
Method used
Examples
Embodiment 1
[0012] Take 1kg of acid leaching vanadium residue obtained by washing with clean water and filtering, wherein the sulfur content is 3.13%, add 1kg of water for stirring and beating, and use a shaking table to separate the residue slurry after beating to obtain 822.36g of concentrate and 822.36g of tailings. 145.24g. After testing, the sulfur content of the concentrate was 0.013%, the sulfur content of the tailings was 19.17%, and the calcium sulfate in the acid leaching residue was effectively removed.
Embodiment 2
[0014] Take 1kg of acid leaching vanadium residue obtained by washing with clean water and filtering, wherein the sulfur content is 3.26%, add 2kg of water for stirring and beating, and use a shaking table to separate the residue slurry after beating to obtain 805.25g of concentrate and 805.25g of tailings. 151.15g. After testing, the sulfur content of the concentrate was 0.020%, the sulfur content of the tailings was 18.57%, and the calcium sulfate in the acid leaching residue was effectively removed.
Embodiment 3
[0016] Take 1kg of acid leaching vanadium residue obtained by washing with clean water and filtering, which contains 1.53% sulfur, add 3kg of water for stirring and beating, and use a shaking table to separate the residue slurry after beating to obtain 860.42g of concentrate and 860.42g of tailings. 76.02g. After testing, the sulfur content of the concentrate was 0.007%, the sulfur content of the tailings was 17.43%, and the calcium sulfate in the acid leaching residue was effectively removed.
[0017] It can be seen from the description of Examples 1 to 3 that after the acid leaching vanadium residue is processed by gravity beneficiation equipment, the sulfur content in the residue is controlled within the range of 0.007% to 0.020%, which shows that calcium sulfate is extracted from acid leaching. Vanadium residues are effectively removed.
PUM
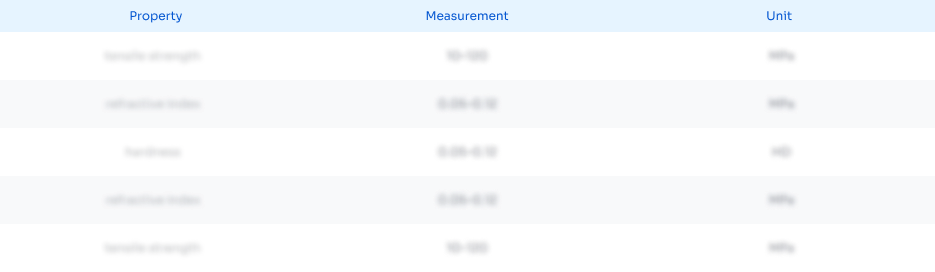
Abstract
Description
Claims
Application Information

- R&D
- Intellectual Property
- Life Sciences
- Materials
- Tech Scout
- Unparalleled Data Quality
- Higher Quality Content
- 60% Fewer Hallucinations
Browse by: Latest US Patents, China's latest patents, Technical Efficacy Thesaurus, Application Domain, Technology Topic, Popular Technical Reports.
© 2025 PatSnap. All rights reserved.Legal|Privacy policy|Modern Slavery Act Transparency Statement|Sitemap|About US| Contact US: help@patsnap.com