Manufacturing method of grid array electrode of crystalline silicon solar cell
A technology of solar cells and array electrodes, which is applied in the direction of final product manufacturing, sustainable manufacturing/processing, circuits, etc., can solve the problems of difficult preparation of micro-array electrodes, large coverage area of silk-screen electrodes, etc., to achieve reduced production costs, superior performance, The effect of improving productivity
- Summary
- Abstract
- Description
- Claims
- Application Information
AI Technical Summary
Problems solved by technology
Method used
Image
Examples
Embodiment 1
[0035] (1) Protective film coating: coating a layer of novolak varnish as a protective film on the surface of a silicon semiconductor coated with a silicon nitride anti-reflection layer; the silicon semiconductor is a single crystal silicon with a p / n junction;
[0036] (2) Laser groove: On the surface of the silicon semiconductor coated with a protective film, an array groove with a depth of 10 μm and a width of 10 μm is carved by laser;
[0037] (3) Surface activation treatment: After the silicon semiconductor with the array groove carved is cleaned by fatty alcohol polyoxyethylene ether sodium sulfate with a mass percentage concentration of 5%, the groove is treated in a HF hydrochloric acid solution with a mass percentage concentration of 5%. Activation was carried out for 5 minutes to obtain a pretreated silicon semiconductor;
[0038] (4) Electroplating: use a conventional electroplating power supply and a conventional electroplating tank, use the cathode of the power su...
Embodiment 2
[0042] (1) protective film coating: coating a layer of alkyd varnish on the surface of a silicon semiconductor coated with a porous silicon dioxide anti-reflection layer as a protective film; the silicon semiconductor is polysilicon with a p / n junction;
[0043] (2) Laser groove: On the surface of the silicon semiconductor coated with a protective film, an array groove with a depth of 20 μm and a width of 20 μm is carved by laser; short circuit;
[0044] (3) Surface activation treatment: After cleaning the silicon semiconductor with array grooves with a mass percentage concentration of 0.5% sodium dodecylbenzene sulfonate, the grooves are aligned in a 5% mass percentage concentration of sodium hydroxide solution. The tank is activated for 0.5min to obtain a pretreated silicon semiconductor;
[0045] (4) Electroplating: use a conventional electroplating power supply and a conventional electroplating tank, use the cathode of the power supply to connect the pretreated semiconduc...
Embodiment 3
[0049] (1) Protective film coating: a layer of nitro varnish is coated on the surface of a silicon semiconductor coated with a titanium dioxide anti-reflection layer as a protective film; the silicon semiconductor is a single crystal silicon with a p / n junction;
[0050] (2) Laser grooving: On the surface of the silicon semiconductor coated with a protective film, an array groove with a depth of 30 μm and a width of 30 μm is carved by laser;
[0051] (3) Surface activation treatment: After the silicon semiconductor with the array grooves is cleaned by sodium dodecyl sulfate with a mass percentage concentration of 2%, the NH 4 HF 2 Activate the groove for 10 minutes in a hydrochloric acid solution to obtain a pretreated silicon semiconductor;
[0052] (4) Electroplating: use a conventional electroplating power supply and a conventional electroplating tank, use the cathode of the power supply to connect the pretreated semiconductor crystal silicon, and connect the anode of the ...
PUM
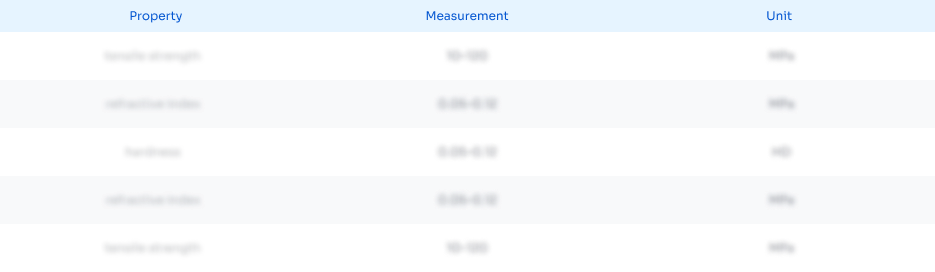
Abstract
Description
Claims
Application Information

- R&D
- Intellectual Property
- Life Sciences
- Materials
- Tech Scout
- Unparalleled Data Quality
- Higher Quality Content
- 60% Fewer Hallucinations
Browse by: Latest US Patents, China's latest patents, Technical Efficacy Thesaurus, Application Domain, Technology Topic, Popular Technical Reports.
© 2025 PatSnap. All rights reserved.Legal|Privacy policy|Modern Slavery Act Transparency Statement|Sitemap|About US| Contact US: help@patsnap.com