Anti-infiltration mucilage for rubber coated fabric products
An anti-leakage and product technology, applied in the field of glue, can solve the problems of complex lamination process, difficult to achieve anti-leakage, affecting appearance quality, etc., to reduce equipment and workshop capital investment, reduce energy consumption, The effect of short production cycle
- Summary
- Abstract
- Description
- Claims
- Application Information
AI Technical Summary
Problems solved by technology
Method used
Examples
Embodiment 1
[0021] 1. Ingredients:
[0022] Neoprene 100kg, sulfur 0.2kg, accelerator M0.2kg, accelerator NA-220.2kg, zinc oxide 2kg, magnesium oxide 2kg, paraffin wax 4kg, pine tar 4kg, antioxidant H0.2kg, Vaseline 4kg, engine oil 10kg, high wear-resistant carbon black 20kg, calcium carbonate 40kg, coloring agent 0.5kg.
[0023] 2. Mixing and tableting:
[0024] First wrap the neoprene rubber on the open mill without holes, then add other prepared materials and knead evenly to produce a sheet.
[0025] 3. Beating:
[0026] First add 206kg of butyl acetate into the beater, and then add the prepared mixed film for beating. After the glue is ready (no grains and lumps), add 19 kg of mixed oil of 50% each of butyl acetate and No. 120 solvent gasoline, and adjust the glue concentration to 15 seconds.
[0027] 4. After passing the inspection, make a spare and use it up within 72 hours. When the room temperature is lower than 18°C, the glue must be kept warm, and the heat preservation temp...
Embodiment 2
[0029] 1. Ingredients:
[0030] Neoprene 110kg, sulfur 0.5kg, accelerator M0.5kg, accelerator NA-220.5kg, zinc oxide 5kg, magnesium oxide 4kg, paraffin wax 5kg, pine tar 5kg, antioxidant H0.5kg, Vaseline 5kg, engine oil 12kg, high wear-resistant carbon black 28kg, calcium carbonate 50kg, coloring agent 0.8kg.
[0031] 2. Mixing and tableting:
[0032] First wrap the neoprene rubber on the open mill without holes, then add other prepared materials and knead evenly to produce a sheet.
[0033] 3. Beating:
[0034] First add 249.5 kg of butyl acetate into the beater, and then add the prepared mixed film for beating. After the glue is ready (no grains or lumps), add 68 kg of mixed oil of 50% each of butyl acetate and No. 120 solvent gasoline, and adjust the glue concentration to 13 seconds.
[0035] 4. After passing the inspection, make a spare and use it up within 72 hours. When the room temperature is lower than 18°C, the glue must be kept warm, and the heat preservation te...
Embodiment 3
[0037] 1. Ingredients:
[0038] Neoprene 120kg, sulfur 0.7kg, accelerator M0.7kg, accelerator NA-220.7kg, zinc oxide 7kg, magnesium oxide 6kg, paraffin wax 6kg, pine tar 6kg, antioxidant H0.7kg, Vaseline 6kg, engine oil 15kg, high wear-resistant carbon black 35kg, calcium carbonate 60kg, coloring agent 1.0kg.
[0039] 2. Mixing and tableting:
[0040] First wrap the neoprene rubber on the open mill without holes, then add other prepared materials and knead evenly to produce a sheet.
[0041] 3. Beating:
[0042] First add 291kg of butyl acetate into the beater, and then add the prepared mixed film for beating. After the glue is well laid (without particles and lumps), add 132 kg of mixed oil of 50% each of butyl acetate and No. 120 solvent gasoline, and adjust the glue concentration to 10 seconds.
[0043] 4. After passing the inspection, make a spare and use it up within 72 hours. When the room temperature is lower than 18°C, the glue must be kept warm, and the heat pres...
PUM
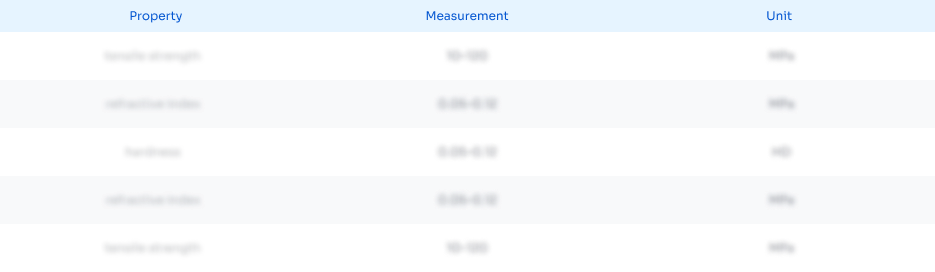
Abstract
Description
Claims
Application Information

- R&D Engineer
- R&D Manager
- IP Professional
- Industry Leading Data Capabilities
- Powerful AI technology
- Patent DNA Extraction
Browse by: Latest US Patents, China's latest patents, Technical Efficacy Thesaurus, Application Domain, Technology Topic, Popular Technical Reports.
© 2024 PatSnap. All rights reserved.Legal|Privacy policy|Modern Slavery Act Transparency Statement|Sitemap|About US| Contact US: help@patsnap.com