Tubular falling film evaporator
A falling film evaporator, tube-type technology, applied in vertical tube evaporators, evaporation, chemical instruments and methods, etc., can solve the problem of large radial damping of steam and heat exchange tubes, low efficiency of tube-type falling film evaporators, removal The problem of incomplete vapor-liquid separation of the bubbler can be solved, so as to reduce the processing cost, strengthen the rigidity, and facilitate maintenance and replacement.
- Summary
- Abstract
- Description
- Claims
- Application Information
AI Technical Summary
Problems solved by technology
Method used
Image
Examples
Embodiment Construction
[0027] attached figure 1 In the first embodiment of the present invention given, the blanks of the upper and lower tube plates 25 and 9 are formed by forging, and after heat treatment, they are subjected to machining such as drilling and other processes, and after being erected, they are assembled with the central circulation tube 2 according to the design requirements. Butt welding. The assembly of the upper and lower tube plates 25, 9, the central circulation tube 2, the stripping drum 18, and the heat exchange tubes 16, baffles 17 and other components are assembled into a heat exchange tube bundle. The heat exchange tube bundle and the upper tube box 20, the heat chamber shell 27, the separation chamber shell 10, the cones 12, 14, the separation chamber lower cone 4 and other components are assembled and welded to form the whole equipment. Among them, the nozzles of the heat exchange tubes 16 are tightly connected with the upper and lower tube plates 25 and 9 by expansion ...
PUM
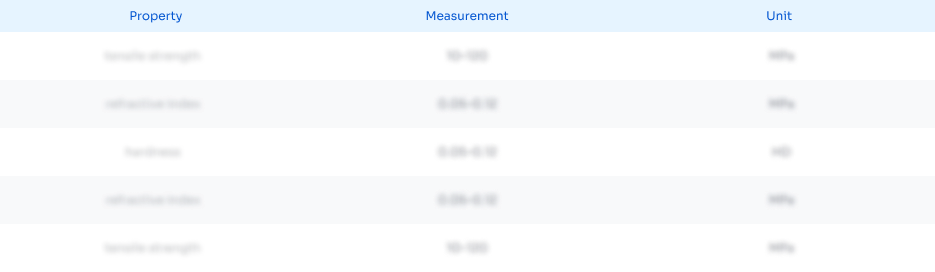
Abstract
Description
Claims
Application Information

- R&D
- Intellectual Property
- Life Sciences
- Materials
- Tech Scout
- Unparalleled Data Quality
- Higher Quality Content
- 60% Fewer Hallucinations
Browse by: Latest US Patents, China's latest patents, Technical Efficacy Thesaurus, Application Domain, Technology Topic, Popular Technical Reports.
© 2025 PatSnap. All rights reserved.Legal|Privacy policy|Modern Slavery Act Transparency Statement|Sitemap|About US| Contact US: help@patsnap.com