Hot-rolled tube billet heating process
A technology of hot-rolled tube and process, which is applied in the field of ring furnace heating process of hot-rolled tube billet, which can solve the problem of uneven wall thickness of blank tube after continuous rolling, without considering the degree of temperature increase of tube billet, and affecting the continuous rolling process And other problems, to achieve the effect of reducing the thickening of the head, reducing the amount of head cutting, and reducing production costs
- Summary
- Abstract
- Description
- Claims
- Application Information
AI Technical Summary
Problems solved by technology
Method used
Examples
Embodiment 1
[0017] Taking the finished product specification as: Φ139.7mm (diameter)×9.17mm (wall thickness) and the steel grade of 30Mn2V as an example, the specification of its core tube blank is Φ200mm (diameter)×3300mm (length), hollow after perforation The specification of the capillary is Φ228mm(diameter)×18.2mm(wall thickness)×830mm(length). The production steps and processes are as follows:
[0018] 1. Ring furnace heating: The tube blank is loaded into the ring furnace from the charging port, placed on the rotary furnace bottom, and driven by the rotary furnace bottom to move from the charging port to the discharging port, and the rotary furnace bottom rotates at a uniform speed , the angular velocity of rotation is 1.73° / min; the steps and processes of heating are as follows:
[0019] (1) Preheating: This step is carried out in the first and second preheating stages. The inner and outer temperatures of the first preheating stage are the same, 1100°C respectively, and the preheat...
Embodiment 2
[0028] Taking the finished product specification as: Φ139.7mm (diameter)×7.72mm (wall thickness) and the steel grade of 30Mn2 as an example, the specification of its core tube blank is: Φ200mm (diameter)×3850mm (length), after perforation The specification of the capillary is Φ227mm (diameter) × 17.2mm (wall thickness) × 1046mm (length). The production steps and processes are as follows:
[0029] 1. Ring furnace heating: The tube blank is loaded into the ring furnace from the charging port, placed on the rotary furnace bottom, and driven by the rotary furnace bottom to move from the charging port to the discharging port, and the rotary furnace bottom rotates at a uniform speed , the angular velocity of rotation is 1.73° / min; the steps and processes of heating are as follows:
[0030] (1) Preheating: This step is carried out in the first and second preheating stages. The inner and outer temperatures of the first preheating stage are the same, 1100°C respectively, and the prehea...
Embodiment 3
[0039] Taking the finished product specification as: Φ244.5mm (diameter)×8.94mm (wall thickness) and the steel grade of 30Mn2 as an example, the specification of its core tube blank is: Φ280mm (diameter)×2750mm (length), after perforation The specification of the capillary is Φ304mm (diameter) × 22.4mm (wall thickness) × 8393mm (length). The production steps and processes are as follows:
[0040] 1. Ring furnace heating: The tube blank is loaded into the ring furnace from the charging port, placed on the rotary furnace bottom, and driven by the rotary furnace bottom to move from the charging port to the discharging port, and the rotary furnace bottom rotates at a uniform speed , the angular velocity of rotation is 1.6° / min; the steps and processes of heating are as follows:
[0041] (1) Preheating: This step is carried out in the first and second preheating stages. The inner and outer temperatures of the first preheating stage are the same, 1100°C respectively, and the preheat...
PUM
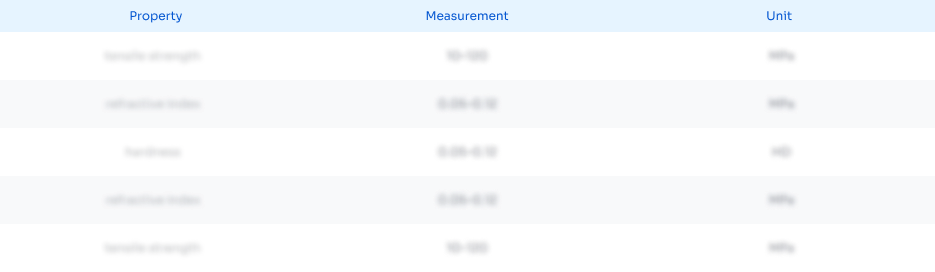
Abstract
Description
Claims
Application Information

- R&D
- Intellectual Property
- Life Sciences
- Materials
- Tech Scout
- Unparalleled Data Quality
- Higher Quality Content
- 60% Fewer Hallucinations
Browse by: Latest US Patents, China's latest patents, Technical Efficacy Thesaurus, Application Domain, Technology Topic, Popular Technical Reports.
© 2025 PatSnap. All rights reserved.Legal|Privacy policy|Modern Slavery Act Transparency Statement|Sitemap|About US| Contact US: help@patsnap.com