Lower flange improved corrugated steel web plate composite box girder and construction method thereof
A technology of corrugated steel webs and combined boxes, which is applied in bridges, bridge materials, bridge construction, etc., can solve the problems of difficulty in ensuring the quality of concrete pouring, reduction of structural bearing capacity and stiffness, difficulty in on-site operation and construction, etc., to achieve pouring The quality is easy to guarantee, the bearing capacity is improved, and the effect of reducing the workload of form work and concrete wet work
- Summary
- Abstract
- Description
- Claims
- Application Information
AI Technical Summary
Problems solved by technology
Method used
Image
Examples
Embodiment Construction
[0016] Below in conjunction with accompanying drawing, structure of the present invention, construction process are described further.
[0017] Compared with the traditional corrugated steel web composite box girder, the invention provides a lower field work load and construction difficulty, easy to ensure the quality of concrete pouring, higher structural bearing capacity, stiffness and crack resistance, and better economic performance. Flange modified corrugated steel web composite box girder. Such as Figure 2 ~ Figure 6 As shown, the box girder is composed of an upper flange concrete slab 1 , a corrugated steel web 3 , a lower flange concrete slab 7 , an upper flange steel plate 4 , a lower flange steel plate 6 and a stud connector 5 . In the lower flange concrete slab 7, steel mesh sheets 9 and prestressed tendon bellows 10 are arranged; similarly, steel bars and prestressed tendon bellows 10 are also arranged in the upper flange concrete slab 1, so that the upper wing ...
PUM
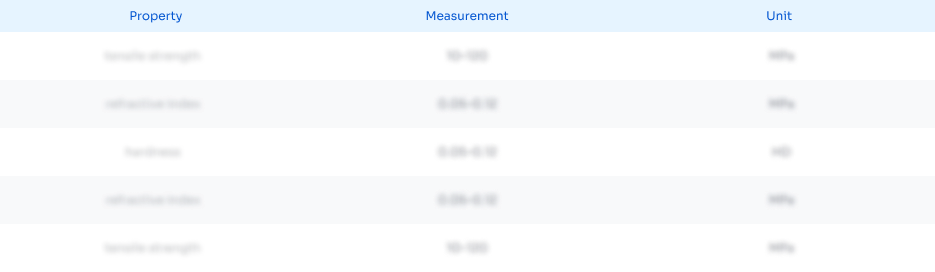
Abstract
Description
Claims
Application Information

- R&D Engineer
- R&D Manager
- IP Professional
- Industry Leading Data Capabilities
- Powerful AI technology
- Patent DNA Extraction
Browse by: Latest US Patents, China's latest patents, Technical Efficacy Thesaurus, Application Domain, Technology Topic, Popular Technical Reports.
© 2024 PatSnap. All rights reserved.Legal|Privacy policy|Modern Slavery Act Transparency Statement|Sitemap|About US| Contact US: help@patsnap.com