Method for controlling form of carbide in bearing steel
A bearing steel and carbide technology, applied in the field of iron and steel metallurgy, can solve the problems of increased magnesium volatilization, low magnesium yield, and difficult control of magnesium content, and achieve the effects of improved distribution, simple process, and easy control
- Summary
- Abstract
- Description
- Claims
- Application Information
AI Technical Summary
Problems solved by technology
Method used
Image
Examples
Embodiment 1
[0044] In this example, the typical bearing steel grade of high-carbon chromium bearing steel is selected, and by changing the composition of the refining slag in the vacuum degassing VD furnace, the content of MgO in the refining slag is mainly increased; the bearings are smelted in the examples) and comparative examples respectively. steel.
[0045] The composition of the bearing steel is shown in Table 1, and the specific composition of the refining slag is shown in Table 2.
[0046] Chemical composition (wt%) of table 1 bearing steel
[0047]
C
Si
mn
Cr
P
S
Mo
Ni
Cu
Mg
Example 1
0.98
0.25
0.37
1.49
0.008
0.012
0.02
0.04
0.06
0.0012-0.0020
Comparative example 2
0.98
0.24
0.33
1.50
0.01
0.007
0.02
0.06
0.11
0.0001-0.0008
[0048] The slag composition (wt%) when tabl...
Embodiment 2
[0069] Effect of different MgO content in refining slag on pearlite lamellar spacing in annealed bearing steel.
[0070] In this embodiment, high-carbon chromium bearing steel, a typical bearing steel steel, is selected. By changing the composition of the refining slag in the vacuum degassing VD furnace, the content of MgO in the refining slag is mainly increased; Smelt bearing steel with refining slag 4 and refining slag 5 (comparative example), wherein refining slag 3 corresponds to material sample 3 (this embodiment), and refining slag 4 and 5 correspond to material samples 4 and 5 (comparative example)
[0071] The composition of the bearing steel is shown in Table 4, and the specific composition of the refining slag is shown in Table 5.
[0072] Chemical composition (wt%) of table 4 bearing steel
[0073]
C
Si
mn
Cr
P
S
Mo
Ni
Cu
Mg
Example 2
0.98
0.25
0.37
1.49
0.008
0.012
0.0...
PUM
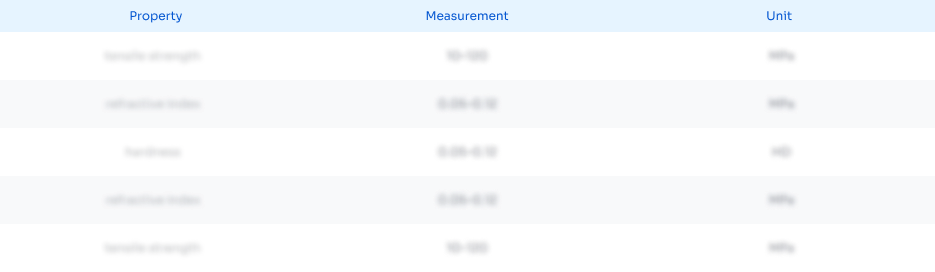
Abstract
Description
Claims
Application Information

- R&D Engineer
- R&D Manager
- IP Professional
- Industry Leading Data Capabilities
- Powerful AI technology
- Patent DNA Extraction
Browse by: Latest US Patents, China's latest patents, Technical Efficacy Thesaurus, Application Domain, Technology Topic, Popular Technical Reports.
© 2024 PatSnap. All rights reserved.Legal|Privacy policy|Modern Slavery Act Transparency Statement|Sitemap|About US| Contact US: help@patsnap.com