Device and method for internal pressure forming of reducer pipes
A technology of variable diameter pipe and internal pressure, which is applied in the field of processing and forming devices for variable diameter pipe fittings, can solve the problems of difficulty in guaranteeing forming accuracy, high processing cost, and numerous working units, and achieve forming accuracy assurance, fewer control components, and simple structure Effect
- Summary
- Abstract
- Description
- Claims
- Application Information
AI Technical Summary
Problems solved by technology
Method used
Image
Examples
specific Embodiment approach 1
[0008] Specific implementation mode one: combine figure 1 Describe this embodiment, this embodiment includes upper punch 1, workbench 2, plunger cylinder 3, high-pressure oil pipe 4, base 5, mold base 6, lower punch 7, die 8, die sleeve 9 and hydraulic booster Device 10, the die 8 is composed of two semi-conical frustums arranged symmetrically, the central axis of the die 8 is provided with a die cavity 8-1, the die 8 is installed in the die sleeve 9, and the upper end surface of the die frame 6 There is a mold cavity 6-1, and the middle section of the die cavity 8-1 is provided with a variable-diameter cavity 8-2, and the base 5, the lower punch 7 and the mold sleeve 9 are installed on the mold base 6 sequentially from bottom to top. 6-1, and the upper end of the lower punch 7 is located in the corresponding die cavity 8-1, the upper punch 1 is set above the die 8, and the lower end of the upper punch 1 is located in the corresponding die cavity In 8-1, an oil hole 1-1 is pr...
specific Embodiment approach 2
[0009] Specific implementation mode two: combination figure 2 This embodiment is described. The difference between this embodiment and the first embodiment is that: the device is further provided with a heating device 11 , and the heating device 11 is set on the outer surface of the mold case 9 . Such a design enables the reduced-diameter pipe fittings made of materials such as magnesium alloys and superhard aluminum alloys with poor room temperature plasticity to be realized by the device of the present invention. Other components and connections are the same as those in the first embodiment.
specific Embodiment approach 3
[0010] Specific implementation mode three: combination figure 2 Describe this embodiment, this embodiment is realized through the following steps: Step 1: First, install the base 5, the lower punch 7 and the die sleeve 9 equipped with the die 8 from bottom to top in the cavity 6 on the mold frame 6- 1, and place the upper end of the lower punch 7 in the corresponding die cavity 8-1; Step 2: load the tube blank 14 from the upper end of the die 8 into the die cavity 8-1; place the upper punch The lower end of the head 1 is placed in the corresponding die cavity 8-1, and the lower end surface of the upper punch 1 closes the upper end surface of the tube blank 14; Step 3: Put the components completed in Step 1 and Step 2 under normal pressure On the working table on the machine, the upper end surface of the working table 2 is connected with the hydraulic cylinder 13 on the ordinary press; Step 4: Drive the working table 2 downward through the hydraulic cylinder 13 to apply force ...
PUM
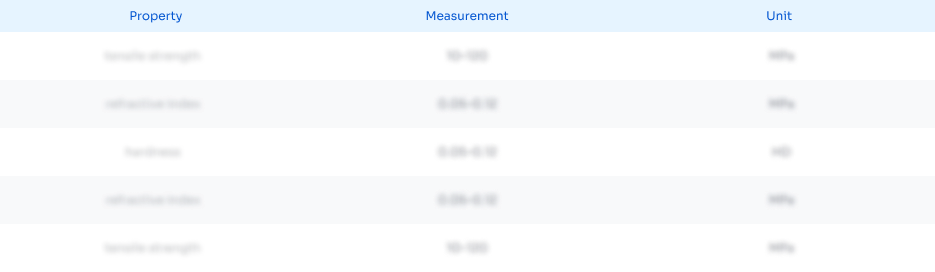
Abstract
Description
Claims
Application Information

- R&D Engineer
- R&D Manager
- IP Professional
- Industry Leading Data Capabilities
- Powerful AI technology
- Patent DNA Extraction
Browse by: Latest US Patents, China's latest patents, Technical Efficacy Thesaurus, Application Domain, Technology Topic, Popular Technical Reports.
© 2024 PatSnap. All rights reserved.Legal|Privacy policy|Modern Slavery Act Transparency Statement|Sitemap|About US| Contact US: help@patsnap.com