Steel-reinforced concrete core column and manufacturing method thereof
A technology of concrete filled steel tube and concrete core, applied in the direction of columns, piers, pillars, etc., to achieve the effect of improving bearing capacity, strong ductility and obvious effect
- Summary
- Abstract
- Description
- Claims
- Application Information
AI Technical Summary
Problems solved by technology
Method used
Image
Examples
Embodiment 1
[0034] Embodiment 1 (the radial section of the concrete core column is "ten" shape)
[0035] Such as figure 1 As shown, the steel frame-concrete filled steel tube core column of the present invention includes steel tube 1, steel plate 2 and concrete 6, at the two ends of the longitudinal limb of the concrete core column, the two ends of the transverse limb and the intersection of the longitudinal limb and the transverse limb Steel pipes 1 are respectively arranged at the points, and the steel pipes are welded into one body by steel plates 2, and the steel plates 2 are welded on the pipe wall of the steel pipes. The outer periphery of the steel pipe 1 and each corner of the concrete core column are provided with longitudinal bars 3 , and each longitudinal bar is bound by stirrups 4 . Concrete 6 is poured inside each steel pipe 1 and in the gap between the steel pipe 1 and the longitudinal reinforcement 3 , and the longitudinal reinforcement 3 is provided with a concrete protec...
Embodiment 2
[0037] Embodiment 2 (the radial section of the concrete core column is "T" shape)
[0038] Such as figure 2 As shown, the steel frame-concrete filled steel tube core column of the present invention includes steel tube 1, steel plate 2 and concrete 6, at the two ends of the concrete core column transverse limb, one end of the longitudinal limb and the intersection point of the longitudinal limb and the transverse limb Steel pipes 1 are respectively arranged at each place, and the steel pipes are welded into one body by steel plates 2, and the steel plates 2 are welded on the pipe wall of the steel pipes. The outer periphery of the steel pipe 1 and each corner of the concrete core column are provided with longitudinal bars 3 , and each longitudinal bar is bound by stirrups 4 . Concrete 6 is poured inside each steel pipe 1 and in the gap between the steel pipe 1 and the longitudinal reinforcement 3 , and the longitudinal reinforcement 3 is provided with a concrete protective la...
Embodiment 3
[0040] Embodiment 3 (the radial section of the concrete core column is "L" shape)
[0041] Such as image 3 As shown, the steel frame-concrete filled steel tube core column of the present invention comprises steel pipe 1, steel plate 2 and concrete 6, at an end of the longitudinal limb of the concrete core column, an end of the transverse limb and the intersection point of the longitudinal limb and the transverse limb ( That is, the corners of the "L" shape are respectively provided with steel pipes 1, and the steel pipes are welded into one body by steel plates 2, and the steel plates 2 are welded on the pipe wall of the steel pipes. The outer periphery of the steel pipe 1 and each corner of the concrete core column are provided with longitudinal reinforcement 3 , and each longitudinal reinforcement is bound by stirrups 4 . Concrete 6 is poured inside each steel pipe 1 and in the gap between the steel pipe 1 and the longitudinal reinforcement 3 , and the longitudinal reinfor...
PUM
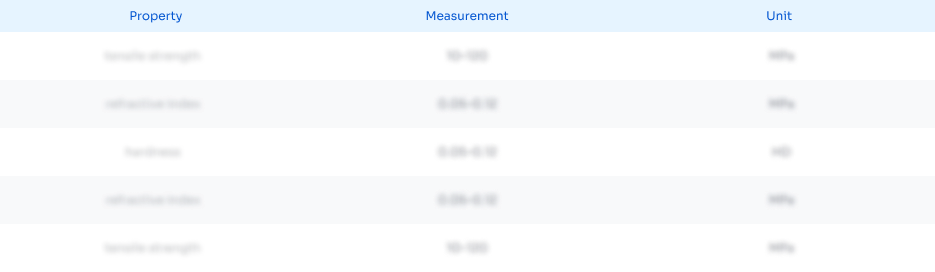
Abstract
Description
Claims
Application Information

- R&D Engineer
- R&D Manager
- IP Professional
- Industry Leading Data Capabilities
- Powerful AI technology
- Patent DNA Extraction
Browse by: Latest US Patents, China's latest patents, Technical Efficacy Thesaurus, Application Domain, Technology Topic, Popular Technical Reports.
© 2024 PatSnap. All rights reserved.Legal|Privacy policy|Modern Slavery Act Transparency Statement|Sitemap|About US| Contact US: help@patsnap.com