Process for continuously producing succinic anhydride through hydrogenation of maleic anhydride
A technology of succinic anhydride and maleic anhydride, which is applied in the field of succinic anhydride production technology, can solve the problems of reducing catalyst reaction performance, inability to react heat, uniformly remove the distribution of reaction liquid, etc., and achieve high equipment utilization rate, simple process flow and high product quality. good quality effect
- Summary
- Abstract
- Description
- Claims
- Application Information
AI Technical Summary
Problems solved by technology
Method used
Image
Examples
Embodiment 1
[0021] Example 1 First, slowly feed nitrogen into the reaction system through the pipeline to replace the air in the fixed bed. The oxygen content to be tested is 99.0%, start to fill the reactor with high-pressure hydrogen to a reaction pressure of 0.9MPa; start the raw material liquid metering pump, and adjust the liquid space velocity of the feed amount to 0.14h -1 , open the heat exchanger to preheat the maleic anhydride solution (THF solution of maleic anhydride, concentration 0.04g / ml) to 35°C, the outlet liquid of the reactor is split at a split ratio of 1 / 2, and the outlet liquid temperature of the circulating heat exchanger is adjusted to 50°C. Gradually adjust the liquid air velocity of the feed amount to 4.2 hours within 2 hours -1 . The reaction solution entering the rectification tower is rectified to obtain the finished product succinic anhydride and solvent, and the solvent is recycled after recovery. Under the above reaction conditions, the activity of the ca...
Embodiment 2
[0022] Example 2 First, nitrogen is slowly introduced into the reaction system through the pipeline to replace the air in the fixed bed, and the oxygen content to be tested is 99.0%, start to fill the reactor with high-pressure hydrogen to a reaction pressure of 8MPa; start the raw material liquid metering pump, and adjust the liquid space velocity of the feed amount to 0.14h -1 , open the heat exchanger to preheat the maleic anhydride solution (gamma-butyrolactone solution of maleic anhydride, concentration 0.08g / ml) to 35°C, the split ratio of the reaction liquid after the reactor is 1 / 3 split, adjust the circulating heat exchanger The outlet temperature was 60°C. Gradually increase the feed amount to normal within 2 hours, and the liquid space velocity of the normal feed amount is 1.4h -1 . The reaction solution entering the rectification tower is rectified to obtain the finished product succinic anhydride and solvent, and the solvent is recycled after recovery. Under the...
Embodiment 3
[0023] Example 3 First, slowly feed nitrogen into the reaction system through the pipeline to replace the air in the fixed bed, the oxygen content to be tested is 99.0%, start to fill the reactor with high-pressure hydrogen to a reaction pressure of 4MPa; start the raw material liquid metering pump, and adjust the liquid space velocity of the feed amount to 0.14h -1 , open the heat exchanger to preheat the maleic anhydride solution (tetrahydrofuran solution of maleic anhydride, concentration 0.08g / ml) to 35°C, the split ratio of the reaction liquid after the reactor is 1 / 4 split, and the temperature of the liquid at the outlet of the circulating heat exchanger is adjusted to 80°C. Gradually increase the feed amount to normal within 2 hours, and the liquid space velocity of the normal feed amount is 2.8h -1 . Part of the reaction liquid is split into the rectification tower through the second-stage reactor to obtain the finished product succinic anhydride and solvent, and the ...
PUM
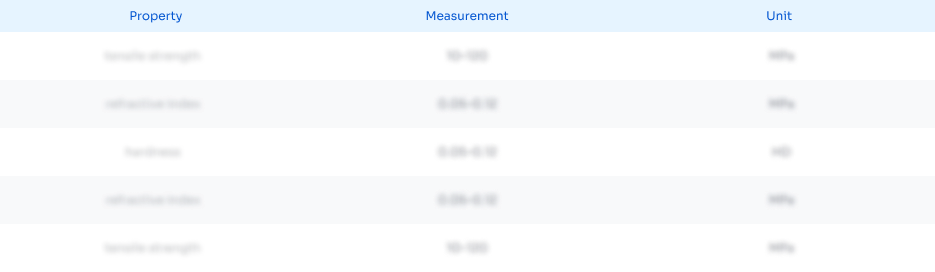
Abstract
Description
Claims
Application Information

- R&D
- Intellectual Property
- Life Sciences
- Materials
- Tech Scout
- Unparalleled Data Quality
- Higher Quality Content
- 60% Fewer Hallucinations
Browse by: Latest US Patents, China's latest patents, Technical Efficacy Thesaurus, Application Domain, Technology Topic, Popular Technical Reports.
© 2025 PatSnap. All rights reserved.Legal|Privacy policy|Modern Slavery Act Transparency Statement|Sitemap|About US| Contact US: help@patsnap.com