Wrist transmission mechanism of stacking robots
A stacking robot and transmission mechanism technology, which is applied in the field of stacking robot wrist transmission mechanism, can solve the problems of high cost and complex structure of wrist transmission mechanism, and achieve the effect of low cost, simple structure and easy conversion
- Summary
- Abstract
- Description
- Claims
- Application Information
AI Technical Summary
Problems solved by technology
Method used
Image
Examples
Embodiment 1
[0091] On the beer production line, the stacking robot is required to pick up the arranged beer cases from the input line and put them on the output line to stack them into stacks. Since the movement direction of finished products on the input and output lines is arranged vertically on the horizontal plane, the robot arm is required to rotate 90 degrees during the handling process. In order to ensure the stability of the movement, the grab box part at the lower part of the robot wrist is required to perform translational movement during the movement; that is, during the handling process of the robot arm rotating 90 degrees, the robot wrist rotates 90 degrees in the opposite direction relative to the swing arm, so that the beer box Only movement occurs, no rotation occurs.
[0092] The specific application of mechanism of the present invention is as follows Figure 7 : the label 101 in the figure is the main body of the stacking robot. The arranged beer cases 104 are input from...
Embodiment 2
[0097] When the input and output pipelines are arranged in parallel, the specific application is as follows (see Figure 9 ): the number 101 in the figure is the main body of the stacking robot. The arranged materials 104 are transported from the input assembly line 102 to the designated position, and are transported by the stacker to the pallet 105 of the output assembly line 103, and finally the whole stack is output; the inventive mechanism is applied to the stacker, and the number of gear teeth Meet Z 2 = Z 6 ,Z 3 = Z 5 (the number of teeth of the first bevel gear (2) is Z 2 , the number of teeth of the second bevel gear (3) is Z 3 , the number of teeth of the third bevel gear (5) is Z 5 , the number of teeth of the fourth bevel gear (6) is Z 6 ), the rotation direction of the wrist rotation axis 7 relative to the swing arm is opposite to the rotation direction of the active rotation axis 9; the movement process of the mechanical arm is shown in Figure 10 , the me...
Embodiment 3
[0099] In some production lines, it is necessary for the grabbing part of the robot to rotate at a certain angle during the movement of the mechanical arm to meet the requirements of the next process, and the transmission ratio of the two pairs of bevel gears can be changed to meet the requirements.
[0100] For example, the number of gear teeth satisfies Z 2 = Z 3 ,Z 5 =1 / 2Z 6 (the number of teeth of the first bevel gear (2) is Z 2 , the number of teeth of the second bevel gear (3) is Z 3 , the number of teeth of the third bevel gear (5) is Z 5 , the number of teeth of the fourth bevel gear (6) is Z 6 ), the mechanical arm rotates 180 degrees counterclockwise. During the movement, the material rotates accordingly. When it reaches the end position, the material rotates 90 degrees counterclockwise.
[0101] Figure 11 It is a three-dimensional schematic diagram of the application of this embodiment on the assembly line, Figure 12 It is the trajectory diagram of the mec...
PUM
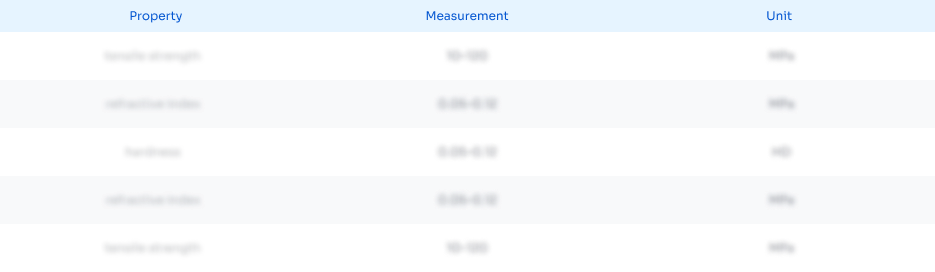
Abstract
Description
Claims
Application Information

- Generate Ideas
- Intellectual Property
- Life Sciences
- Materials
- Tech Scout
- Unparalleled Data Quality
- Higher Quality Content
- 60% Fewer Hallucinations
Browse by: Latest US Patents, China's latest patents, Technical Efficacy Thesaurus, Application Domain, Technology Topic, Popular Technical Reports.
© 2025 PatSnap. All rights reserved.Legal|Privacy policy|Modern Slavery Act Transparency Statement|Sitemap|About US| Contact US: help@patsnap.com