Pressure sensor structure of compound diaphragm
A pressure sensor and composite diaphragm technology, which is applied in the direction of elastic deformation meter-type fluid pressure measurement, etc., can solve the problems of immature, unclear, and stuck in the experimental stage of device preparation, so as to reduce the complexity of the process and reduce the size of the membrane. Sheet deflection, the effect of expanding the measuring range
- Summary
- Abstract
- Description
- Claims
- Application Information
AI Technical Summary
Problems solved by technology
Method used
Image
Examples
Embodiment Construction
[0025] see Figure 1-Figure 3 Shown, a kind of composite diaphragm pressure sensor structure of the present invention comprises:
[0026] A monocrystalline silicon layer 1, one side of the monocrystalline silicon layer 1 is concave, and the bottom surface of the concave monocrystalline silicon layer 1 is a flat structure 3 (such as figure 1 ); the bottom surface of the concave monocrystalline silicon layer 1 is an island structure 4; the island structure 4 is a single island (such as figure 2 ), Shuangdao (such as image 3 ) or a multi-island structure (not shown); the island structure 4 is a square island, rectangular island or circular island structure;
[0027] A porous silicon layer 2, the porous silicon layer 2 grows on the concave inner surface of the monocrystalline silicon layer 1, thus forming a planar type 3 structure (such as figure 1 ), island structure 4 (such as figure 2 , image 3 ); The island structure 4 is a single island (such as figure 2 ), Shuangd...
PUM
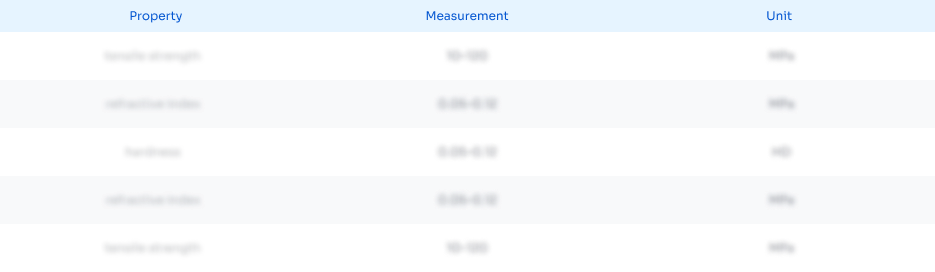
Abstract
Description
Claims
Application Information

- Generate Ideas
- Intellectual Property
- Life Sciences
- Materials
- Tech Scout
- Unparalleled Data Quality
- Higher Quality Content
- 60% Fewer Hallucinations
Browse by: Latest US Patents, China's latest patents, Technical Efficacy Thesaurus, Application Domain, Technology Topic, Popular Technical Reports.
© 2025 PatSnap. All rights reserved.Legal|Privacy policy|Modern Slavery Act Transparency Statement|Sitemap|About US| Contact US: help@patsnap.com