Advanced treatment method for coal chemical wastewater
A technology for advanced treatment of coal chemical wastewater, applied in natural water treatment, chemical instruments and methods, biological water/sewage treatment, etc. It can reduce the production of excess sludge, save operating costs, and save processing costs.
- Summary
- Abstract
- Description
- Claims
- Application Information
AI Technical Summary
Problems solved by technology
Method used
Examples
specific Embodiment approach 1
[0009] Specific Embodiment 1: This embodiment is used for the advanced treatment of coal chemical industry wastewater according to the following steps: 1. Add biological filler and activated sludge to the reactor in turn; 2. Add coal chemical industry wastewater and methanol production wastewater to be treated, Form the mixed wastewater of coal chemical industry and methanol production to be treated, and then add KH to the mixed wastewater of coal chemical industry and methanol production to be treated according to the ratio of COD:P=100:1 2 PO 4 ; 3. Air is introduced into the reactor until the concentration of dissolved oxygen in the mixed wastewater of coal chemical industry and methanol production to be treated is 3-5mg / L; 4. The reactor is aerated for 23 hours, and then statically settled for 1 hour, and the coal is completed. Advanced treatment of chemical wastewater; wherein the amount of biological filler added in step 1 is 25% to 35% of the reactor volume, and the bio...
specific Embodiment approach 2
[0013] Embodiment 2: This embodiment differs from Embodiment 1 in that the amount of biological filler added in step 1 is 28% to 32% of the reactor volume. Other steps and parameters are the same as those in Embodiment 1.
specific Embodiment approach 3
[0014] Embodiment 3: The difference between this embodiment and Embodiment 1 is that the amount of biological filler added in step 1 is 30% of the volume of the reactor. Other steps and parameters are the same as those in Embodiment 1.
PUM
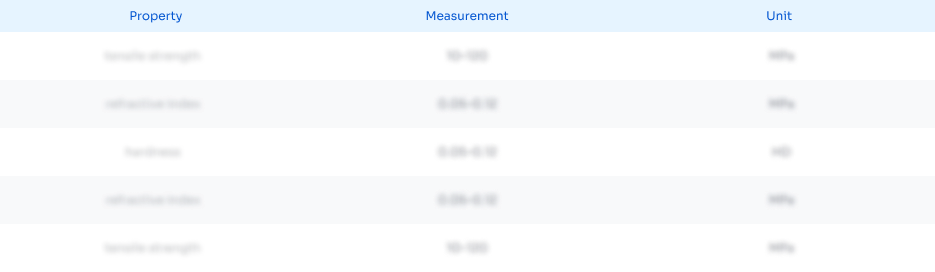
Abstract
Description
Claims
Application Information

- R&D Engineer
- R&D Manager
- IP Professional
- Industry Leading Data Capabilities
- Powerful AI technology
- Patent DNA Extraction
Browse by: Latest US Patents, China's latest patents, Technical Efficacy Thesaurus, Application Domain, Technology Topic, Popular Technical Reports.
© 2024 PatSnap. All rights reserved.Legal|Privacy policy|Modern Slavery Act Transparency Statement|Sitemap|About US| Contact US: help@patsnap.com