Fiber reinforced composite dot matrix core board mold and wet method preparation process
A composite material and fiber-reinforced technology, which is applied in the mold and wet preparation process of fiber-reinforced composite lattice sandwich panels, can solve the problem of fiber-reinforced composite lattice sandwich panels without fiber-reinforced composite lattice sandwich cores. board and other issues, to achieve the effect of low cost, high specific strength, and convenient operation
- Summary
- Abstract
- Description
- Claims
- Application Information
AI Technical Summary
Problems solved by technology
Method used
Image
Examples
specific Embodiment approach 1
[0014] Specific implementation mode one: as Figure 1~2 As shown, the mold of the fiber-reinforced composite lattice sandwich panel in this embodiment includes a plurality of mold units 1 and two fixing bars 2, the cross-section of each mold unit 1 is non-isosceles trapezoidal, each mold There are multiple pairs of first semicircular through-holes 1-1 on an inclined surface of the monomer 1, and the first semicircular through-holes 1-1 communicate with the upper and lower surfaces of the mold monomer 1, and each pair of first semicircular through-holes 1-1 The through holes 1-1 are arranged in a figure-eight shape, and the included angles between the centerlines of the first semicircular through holes 1-1 and the horizontal line are equal. A second semicircular through hole 1-2 is opened at the corresponding position of the circular through hole 1-1, and the centerline of the second semicircular through hole 1-2 is aligned with the corresponding pair of first semicircular thro...
specific Embodiment approach 2
[0015] Specific implementation mode two: as figure 1 As shown, the mold in this embodiment also includes a plurality of hard metal strips 3 with a circular cross section, and a third circular through hole 1-3 is opened at the center of each mold unit 1 along the length direction. A circular hard metal strip 3 is fixed in the third circular through hole 1-3 on each mold unit 1 . Such a design can prevent the mold unit 1 from being deformed along the length direction and play the role of a skeleton.
[0016] Other components and connections are the same as those in the first embodiment.
specific Embodiment approach 3
[0017] Specific implementation mode three: as figure 1 As shown, the wet process steps of the fiber-reinforced composite lattice sandwich panel in this embodiment are as follows:
[0018] Step 1, mold treatment: clean the surface of the mold with acetone solution, and then treat the outer surface of the mold with a release agent;
[0019] Step 2. Fix the mold: Fix the mold with a fixture;
[0020] Step 3, rolling fiber column: roll the fiber column with prepreg, keep the fiber direction the same as the axial direction of the fiber column, the diameter of the rolled fiber column is the same as the first circular through hole 1-1-1 and the second The diameters of the circular through holes 1-2-1 are the same, and the number of rolled fiber columns is the sum of the number of the first circular through holes 1-1-1 and the number of the second circular through holes 1-2-1 , the length of the rolled fiber column is 40-50 mm longer than the length of the first circular through hol...
PUM
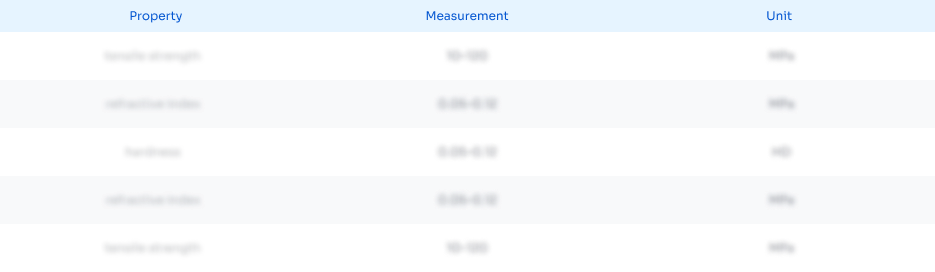
Abstract
Description
Claims
Application Information

- R&D
- Intellectual Property
- Life Sciences
- Materials
- Tech Scout
- Unparalleled Data Quality
- Higher Quality Content
- 60% Fewer Hallucinations
Browse by: Latest US Patents, China's latest patents, Technical Efficacy Thesaurus, Application Domain, Technology Topic, Popular Technical Reports.
© 2025 PatSnap. All rights reserved.Legal|Privacy policy|Modern Slavery Act Transparency Statement|Sitemap|About US| Contact US: help@patsnap.com