Centrifugal cast tube die and manufacturing technique thereof
A technology of centrifugal casting pipe and manufacturing process, which is applied in the field of metallurgy, can solve problems such as scrapping, cracks on the inner wall of the pipe mold, and waste products, and achieve the effects of improving thermal fatigue resistance, improving service life, and extending service life
- Summary
- Abstract
- Description
- Claims
- Application Information
AI Technical Summary
Problems solved by technology
Method used
Image
Examples
Embodiment Construction
[0019] The invention discloses a structure and a manufacturing process of a cast pipe mold, so as to improve the service life of the pipe mold in centrifugal casting and reduce the probability of waste products produced by steel pipes in production.
[0020] Cast pipe mold structure among the present invention has following characteristics:
[0021] The casting pipe mold is made of metal material, and a heat-resistant mold steel composite layer is attached on the inner surface of the pipe wall of the casting pipe mold.
[0022] The heat-resistant die steel composite layer is made of 20CrMoWV material. The weight percentage of each alloy element in the heat-resistant die steel is C: 0.16-0.24; Si: 0.20-0.50; Mn: 0.30-0.60; P : ≤0.015; S≤0.012; Cr: 2.0~2.6; Mo: 0.40~1.0; W: 0.60~1.10; V: 0.03~0.06, the thickness of the composite layer is not less than 20 mm.
[0023] The outer tube wall is made of ordinary heat-resistant steel or low-alloy heat-resistant steel.
[0024] When t...
PUM
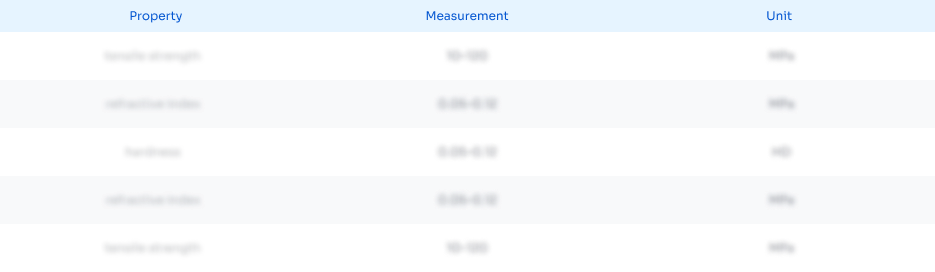
Abstract
Description
Claims
Application Information

- R&D Engineer
- R&D Manager
- IP Professional
- Industry Leading Data Capabilities
- Powerful AI technology
- Patent DNA Extraction
Browse by: Latest US Patents, China's latest patents, Technical Efficacy Thesaurus, Application Domain, Technology Topic, Popular Technical Reports.
© 2024 PatSnap. All rights reserved.Legal|Privacy policy|Modern Slavery Act Transparency Statement|Sitemap|About US| Contact US: help@patsnap.com