Method for recovering condensation water in production process of gas concrete and recovery system thereof
A kind of air-entrained concrete and production process technology, applied in the direction of ceramic molding machines, manufacturing tools, etc., can solve the problems of wasting energy and water resources, and achieve the effects of alleviating corrosion, ensuring quality, and using energy in a scientific and reasonable way
- Summary
- Abstract
- Description
- Claims
- Application Information
AI Technical Summary
Problems solved by technology
Method used
Image
Examples
Embodiment 1
[0031] (1) The 1.25MPa saturated steam produced by the boiler is sent into the autoclave where the aerated concrete slab is placed to heat the aerated concrete product, and the saturated steam is cooled to condensed water through heat exchange;
[0032] (2) Send the condensed water discharged from the autoclave to a plurality of secondary heat user devices containing materials therein, and use the waste heat of the condensed water to preheat the materials, and the condensed water is passed through Heat exchange and cooling to secondary condensed water;
[0033] (3) The secondary condensed water discharged from the secondary heat user device is purified and treated to meet boiler feed water requirements, and then sent to the boiler in the step (1) for recycling.
[0034] After testing: the recovery rate of condensed water produced by the autoclave reaches 93.3%, and the utilization rate of waste heat reaches 92.6%.
Embodiment 2
[0036] (1) The 1.28Mpa saturated steam produced by the boiler is sent into the autoclave that is placed with the aerated concrete block to heat the aerated concrete product, and the saturated steam is cooled to condensed water through heat exchange;
[0037] (2) Send the condensed water discharged from the autoclave to a plurality of secondary heat user devices containing materials therein, and use the waste heat of the condensed water to preheat the materials, and the condensed water is passed through Heat exchange and cooling to secondary condensed water;
[0038] (3) The secondary condensed water discharged from the secondary heat user device is purified and treated to meet boiler feed water requirements, and then sent to the boiler in the step (1) for recycling.
[0039] After testing: the recovery rate of condensed water produced by the autoclave reaches 92.8%, and the utilization rate of waste heat reaches 91.3%.
Embodiment 3
[0041] (1) The 1.30Mpa saturated steam produced by the boiler is sent into the autoclave where the aerated concrete slab is placed to heat the aerated concrete product, and the saturated steam is cooled to condensed water through heat exchange;
[0042] (2) Send the condensed water discharged from the autoclave to a plurality of secondary heat user devices containing materials therein, and use the waste heat of the condensed water to preheat the materials, and the condensed water is passed through Heat exchange and cooling to secondary condensed water;
[0043](3) After the secondary condensed water discharged from the secondary heat user device is purified to meet the boiler feed water requirements, it is sent to the boiler in the step (1) for recycling.
[0044] After testing: the recovery rate of condensed water produced by the autoclave reaches 93.5%, and the utilization rate of waste heat reaches 90.3%.
PUM
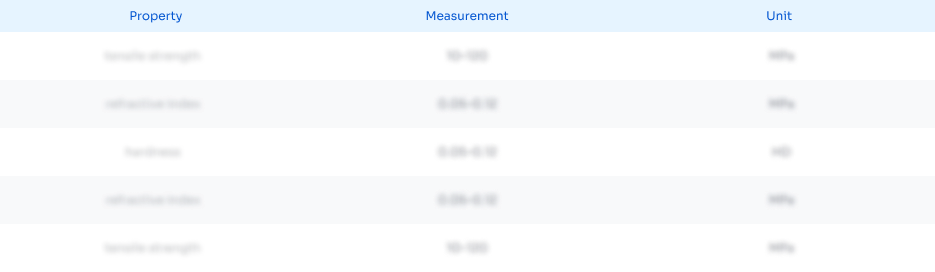
Abstract
Description
Claims
Application Information

- R&D Engineer
- R&D Manager
- IP Professional
- Industry Leading Data Capabilities
- Powerful AI technology
- Patent DNA Extraction
Browse by: Latest US Patents, China's latest patents, Technical Efficacy Thesaurus, Application Domain, Technology Topic, Popular Technical Reports.
© 2024 PatSnap. All rights reserved.Legal|Privacy policy|Modern Slavery Act Transparency Statement|Sitemap|About US| Contact US: help@patsnap.com