Welding equipment and welding method
A welding device and welding wire technology, applied in welding equipment, welding equipment, tin feeding devices, etc., can solve problems such as poor appearance, errors, and winding traces
- Summary
- Abstract
- Description
- Claims
- Application Information
AI Technical Summary
Problems solved by technology
Method used
Image
Examples
Embodiment Construction
[0062] First, according to Figure 1 to Figure 4 , the first embodiment of the welding device of the present invention will be described in detail.
[0063] The welding device of the present invention generally includes: a welding torch 1, which imparts heat energy to the welding site; a welding wire supply unit 2, which supplies filler wire F to the welding site; and a tracking unit 3, which controls the movement trajectory of the welding torch 1 and the welding wire supply unit 2 Follow the welding line Y; the tracking unit 3 has a contact 30A or 30B, and the contact 30A or 30B is arranged in a manner that can advance and retreat or can rotate, and elastically contacts the joint object W; the filler wire is supplied to the welding site by the welding wire supply unit 2 F, and the heat energy is given by the welding torch 1, and at the same time, the contact 30A or 30B of the tracking unit 3 is elastically contacted with the object W to be joined, so that the welding torch 1 ...
PUM
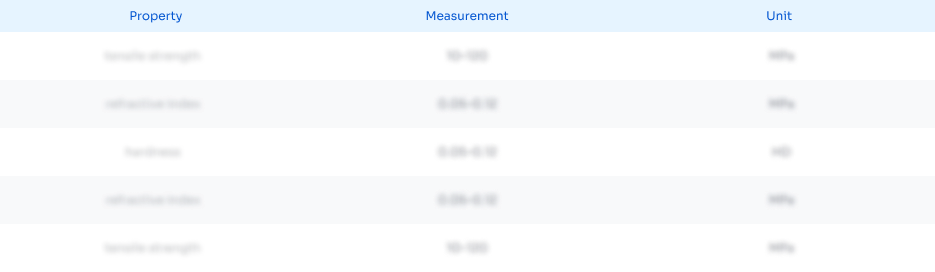
Abstract
Description
Claims
Application Information

- R&D Engineer
- R&D Manager
- IP Professional
- Industry Leading Data Capabilities
- Powerful AI technology
- Patent DNA Extraction
Browse by: Latest US Patents, China's latest patents, Technical Efficacy Thesaurus, Application Domain, Technology Topic, Popular Technical Reports.
© 2024 PatSnap. All rights reserved.Legal|Privacy policy|Modern Slavery Act Transparency Statement|Sitemap|About US| Contact US: help@patsnap.com