Coating modified material of nano calcium carbonate and modification method thereof
A technology of nano-calcium carbonate and modified materials, which is applied in the treatment of fibrous fillers and dyed high-molecular organic compounds. Dispersion performance, improvement of physical and chemical properties, and the effect of improving dispersibility
- Summary
- Abstract
- Description
- Claims
- Application Information
AI Technical Summary
Problems solved by technology
Method used
Image
Examples
Embodiment 1
[0035] Add 25KG nano calcium carbonate in QMJ200 vertical ball mill, then add 50KG deionized water and carry out ball milling for 5 minutes, the carboxylated styrene-butadiene emulsion (wherein the volume ratio of carboxylated styrene-butadiene emulsion and nano-calcium carbonate is respectively 13%, Diluted deionized water (75KG) was added to the ball mill for ball milling for 90 minutes, and the ball mill speed was 45 r / min .
[0036] The slurry after ball milling is filtered through a 800-type filter press. Then put it into a fully automatic pusher kiln for drying.
[0037] The drying temperature is 200°C, and the pushing speed is 5 minutes / cycle. The dried material is dispersed in a 100L vertical internal screw mixer with a mixer frequency of 1400
[0038] The dispersed material is sampled and sent to TEM for deposition volume test.
[0039] see figure 1 , The edges and corners of the powder particles are blunted and close to spherical, not easy to agglomerate, and ha...
Embodiment 2
[0043] Add 25KG nano-calcium carbonate in QMJ200 vertical ball mill, then add carboxypolybutadiene (the volume ratio of carboxypolybutadiene and nano-calcium carbonate is 13%), then add 50L toluene, ball mill 90 minutes, ball mill speed 45 r / min .
[0044] The slurry after ball milling is filtered through an 800-type filter press. Then put it into a fully automatic pusher kiln for drying.
[0045] The drying temperature is 200°C, and the pushing speed is 5 minutes / cycle. The dried material is dispersed in a 100L vertical internal screw mixer with a mixer frequency of 1400
[0046] The dispersed material is sampled and sent to TEM for deposition volume test.
[0047] see figure 2 , the edges and corners of the coated particles are passivated, and the appearance of the particles is gradually approaching spherical. Because carboxypolybutadiene itself is relatively viscous, the adhesion between the coated particles is more serious.
[0048] see Figure 4 , FT-IR spectrum of...
PUM
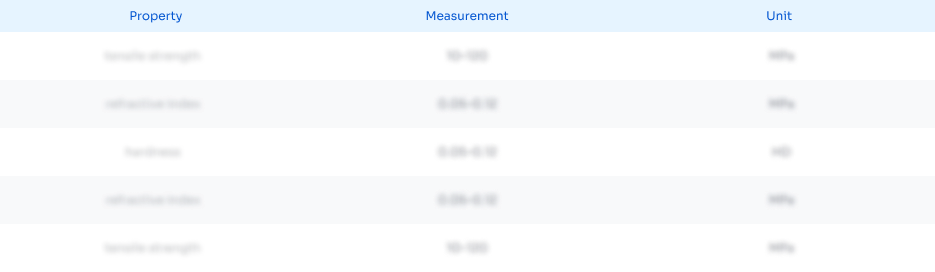
Abstract
Description
Claims
Application Information

- R&D
- Intellectual Property
- Life Sciences
- Materials
- Tech Scout
- Unparalleled Data Quality
- Higher Quality Content
- 60% Fewer Hallucinations
Browse by: Latest US Patents, China's latest patents, Technical Efficacy Thesaurus, Application Domain, Technology Topic, Popular Technical Reports.
© 2025 PatSnap. All rights reserved.Legal|Privacy policy|Modern Slavery Act Transparency Statement|Sitemap|About US| Contact US: help@patsnap.com