Adjustable-pressure automatic stirring liquid supply system
A self-stirring, adjustable pressure technology, applied in metal processing machinery parts, maintenance and safety accessories, metal processing equipment, etc., can solve the problems of time-consuming and expensive valve replacement, inappropriate use of centrifugal pumps, and reduced processing efficiency. Achieve the effects of improving pump fluid quality, reducing clogging and increasing production efficiency
- Summary
- Abstract
- Description
- Claims
- Application Information
AI Technical Summary
Problems solved by technology
Method used
Image
Examples
specific Embodiment approach 1
[0020] Specific implementation mode one: refer to figure 1 , the specific embodiment adopts the following technical solutions: it is composed of a locking mechanism 1, a constant pressure cylinder 2, a dial 3, a positioning cylinder support 4, a sludge pump 5, a slurry bucket 6, a filter 7 and a grinding and polishing machine 8 Composition, the filter 7 and the sludge pump 5 are arranged on the upper end of the slurry tank 6, and the outlet pipe is divided into two ways at the water outlet through the sludge pump 5, one way is connected with the constant pressure cylinder 2, and the other way is directly along the wall of the slurry tank 6. The position close to the bottom of the bucket is connected tangentially to the inside of the bucket, and the outlet pipe at the bottom of the constant pressure cylinder 2 is connected to the working area of the grinding disc of the grinding and polishing machine 8, and the slurry collector inside the grinding and polishing machine 8 is co...
specific Embodiment approach 2
[0022] Specific embodiment two: the difference between this specific embodiment and specific embodiment one is: its abrasive grain is 1000# cubic boron carbide abrasive grain, adds certain additive and pure water and mixes into grinding liquid (abrasive material concentration 20%) , the length of the constant pressure cylinder 2 is selected to be 60 cm, the inclination angle of the constant pressure cylinder 2 is 75 degrees, the grinding liquid can stably flow out from the water outlet of the constant pressure cylinder 2, and the measured flow rate is 0.21 L / min. Other components and connections are the same as those in the first embodiment.
specific Embodiment approach 3
[0023] Specific embodiment three: the difference between this specific embodiment and specific embodiment one is: its abrasive grain is 1500# cubic boron carbide abrasive grain, adds certain additive and deionized water and mixes into grinding liquid (abrasive material concentration 40% ), the length of the constant pressure cylinder 2 is selected to be 90 cm, and the inclination angle of the constant pressure cylinder 2 is 75 degrees. Other components and connections are the same as those in the first embodiment.
PUM
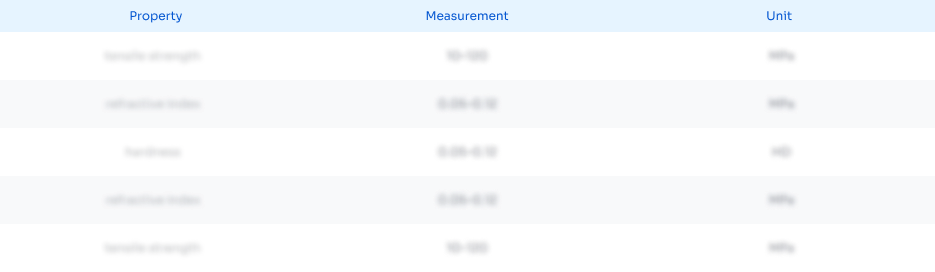
Abstract
Description
Claims
Application Information

- Generate Ideas
- Intellectual Property
- Life Sciences
- Materials
- Tech Scout
- Unparalleled Data Quality
- Higher Quality Content
- 60% Fewer Hallucinations
Browse by: Latest US Patents, China's latest patents, Technical Efficacy Thesaurus, Application Domain, Technology Topic, Popular Technical Reports.
© 2025 PatSnap. All rights reserved.Legal|Privacy policy|Modern Slavery Act Transparency Statement|Sitemap|About US| Contact US: help@patsnap.com