Process to manufacture 2-chloro-1,1,1,2-tetrafluoropropane (HCFC-244bb)
A technology of tetrafluoropropane and tetrafluoropropene, applied in the field of preparing HCFC-244bb, can solve the problems of promoting the formation of by-products, reducing the conversion rate, and difficult to control
- Summary
- Abstract
- Description
- Claims
- Application Information
AI Technical Summary
Problems solved by technology
Method used
Examples
Embodiment 1
[0044] Demonstrate the continuous liquid of 2-chloro-3,3,3-trifluoropropene (HCFO-1233xf)+HF→2-chloro-1,1,1,2-tetrafluoropropane (HCFC-244bb) when HCl is fed continuously phase fluorination reaction. The fluorination catalyst in this experiment was SbCl 5 .
[0045] Equipped with a catalyst stripper, 2 inch ID (inside diameter) packed column and used to return entrained catalyst, some unreacted HF and some unreacted HCFO-1233xf to the reactor when the system is operating in continuous reaction mode Condenser Teflon TM The lined liquid phase reactor (Teflon is a trademark of E.I. duPont deNemours & Co) contained 6500 grams of SbCl 5 . The reactor was 2.75 inches ID x 36 inches L (length) and was not equipped with a mixer / stirrer. The reactor was heated to about 85°C-87°C. Then by adding 1500 g HF followed by 1500 g Cl 2 to activate the catalyst. HCl produced by the fluorination of the catalyst raises the pressure of the reaction system to about 100 psig, where it is con...
Embodiment 2
[0047] The stream from the top of the catalyst stripper in Example 1 mainly comprising HCFC-244bb, unreacted HF and HCl is fed to a conventional distillation column where the HCl is recovered and / or recycled back to the liquid phase reactor To aid in mixing, maintaining pressure and bringing out product.
Embodiment 3
[0049] A 2000 gallon industrial scale reactor was charged with antimony pentachloride catalyst. HCFO-1233xf and HF are continuously fed into the reaction vessel. HF is fed in excess. Hydrogen chloride was added as an additional component to aid in mixing and to aid in the evaporation of the product. HCFC-244bb, HF and hydrogen chloride leave the vessel and are recovered.
PUM
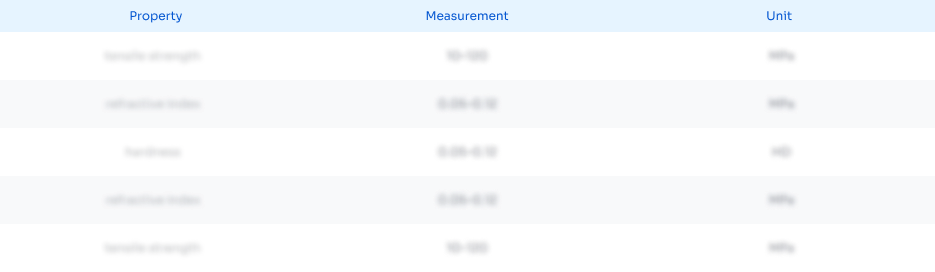
Abstract
Description
Claims
Application Information

- R&D
- Intellectual Property
- Life Sciences
- Materials
- Tech Scout
- Unparalleled Data Quality
- Higher Quality Content
- 60% Fewer Hallucinations
Browse by: Latest US Patents, China's latest patents, Technical Efficacy Thesaurus, Application Domain, Technology Topic, Popular Technical Reports.
© 2025 PatSnap. All rights reserved.Legal|Privacy policy|Modern Slavery Act Transparency Statement|Sitemap|About US| Contact US: help@patsnap.com