Manufacture process of thermal insulation bucket of hard composite graphite felt for single crystal furnace
A composite graphite, thermal insulation technology, applied in the direction of single crystal growth, manufacturing tools, applications, etc., can solve the problems of poor anti-oxidation performance, insufficient accuracy, and poor adhesion, achieve easy heating and cooling, increase service life, Not easy to layer effect
- Summary
- Abstract
- Description
- Claims
- Application Information
AI Technical Summary
Problems solved by technology
Method used
Image
Examples
Embodiment Construction
[0026] like figure 1 As shown, high-purity graphite felt (produced by Gansu Haoshi Carbon Fiber Co., Ltd.) treated at 2200° C. was selected as the green body material. According to the corresponding single crystal furnace size (16#, 18#, 20#, 24#), the mold is made, and the blank material is wound by an automatic winding machine at a rotation rate of 1 circle / 30s while brushing the adhesive and winding it to make the shape. The felt layer has a tight structure and is not easy to delaminate; then after curing, that is, in a high-temperature purification furnace, the green body is heated to 210 °C at a heating rate of 30 °C / h and cooled to 60 °C for 2 hours. The green body is solidified and formed; the green body is purified again, that is, N is introduced into the high temperature purification furnace. 2 with Cl 2 The gas is heated up to 2200°C at a heating rate of 30°C / h for purification treatment; the green body after purification treatment is formed; the surface is polishe...
PUM
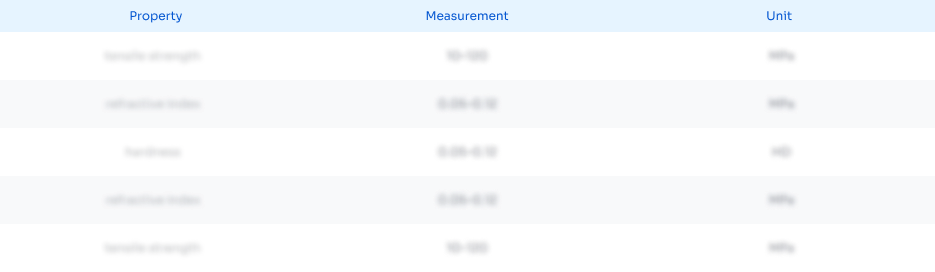
Abstract
Description
Claims
Application Information

- Generate Ideas
- Intellectual Property
- Life Sciences
- Materials
- Tech Scout
- Unparalleled Data Quality
- Higher Quality Content
- 60% Fewer Hallucinations
Browse by: Latest US Patents, China's latest patents, Technical Efficacy Thesaurus, Application Domain, Technology Topic, Popular Technical Reports.
© 2025 PatSnap. All rights reserved.Legal|Privacy policy|Modern Slavery Act Transparency Statement|Sitemap|About US| Contact US: help@patsnap.com