Grinding sheet for disc grinder and manufacturing method thereof
A manufacturing method and disc refiner technology, which are applied in manufacturing tools, pulp beating/refining methods, papermaking, etc., can solve the problems of short service life, low yield of grinding discs, and low hardness, so as to improve yield and reduce price, waste reduction effect
- Summary
- Abstract
- Description
- Claims
- Application Information
AI Technical Summary
Problems solved by technology
Method used
Image
Examples
Embodiment
[0027] In this embodiment, a kind of grinding plate for a disc grinder has a structure such as figure 1 As shown, it includes the grinding teeth 1 and the grinding plate base 2 which have been processed and formed twice respectively. Around the central axis of the grinding plate base 2, the grinding teeth 1 are evenly arranged on the grinding plate base 2 in a state of multiple concentric circles. Slurry baffles 3 are arranged between the teeth 1 , and the baffles 3 located on the same circle form a helical slurry line on the surface of the base body 2 of the grinding disc.
[0028] Such as figure 2 As shown, the central hole of the base body 2 of the grinding disc is a cylindrical hole with an inverted cone structure on the upper part, and the setting of the inverted cone structure is beneficial to the flow of pulp in the grinding disc.
[0029] Among the above-mentioned grinding discs, the material of the grinding teeth 1 is a wear-resistant material with high hardness and...
PUM
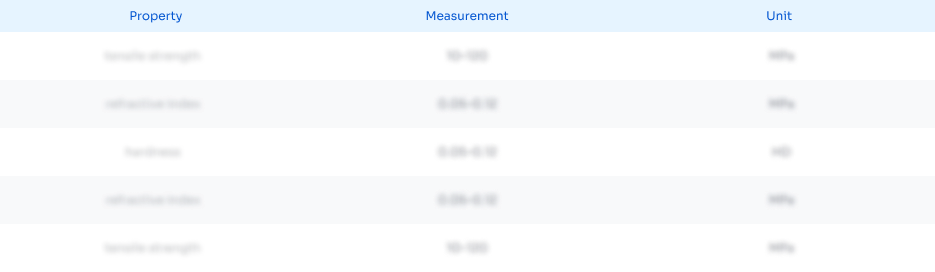
Abstract
Description
Claims
Application Information

- R&D
- Intellectual Property
- Life Sciences
- Materials
- Tech Scout
- Unparalleled Data Quality
- Higher Quality Content
- 60% Fewer Hallucinations
Browse by: Latest US Patents, China's latest patents, Technical Efficacy Thesaurus, Application Domain, Technology Topic, Popular Technical Reports.
© 2025 PatSnap. All rights reserved.Legal|Privacy policy|Modern Slavery Act Transparency Statement|Sitemap|About US| Contact US: help@patsnap.com