Carbon-manganese composite microalloyed steel for engineering machinery and preparation method thereof
A technology of construction machinery and micro-alloying, applied in the direction of temperature control, furnace type, furnace, etc., to reduce center porosity and segregation, stabilize hardenability, and increase equiaxed crystals of billets
- Summary
- Abstract
- Description
- Claims
- Application Information
AI Technical Summary
Problems solved by technology
Method used
Image
Examples
Embodiment 1
[0038] Example 1: 15B36Cr steel
[0039] 1. The weight percent of the chemical composition of the steel is: C0.37 Si0.22 Mn1.25 P0.014 S0.009 B0.0014 Al0.025Ti0.03Ti / N=3.5; the balance is Fe and trace impurities.
[0040] 2. The process route is:
[0041] Batching→electric furnace smelting→tapping from eccentric furnace bottom→deoxidation and alloying in LF furnace→adding iron boron to adjust boron composition→vacuum refining furnace degassing→full protection casting of billet continuous casting machine→rolled product specification Φ70mm→inspection and storage.
[0042] 3. The main process measures of the preparation method
[0043] (1) The proportion of molten iron in the furnace steel material structure reaches 40-60%; no high-phosphorus and sulfur scrap steel such as slag steel and tank side iron are added to the batching.
[0044] (2) The smelting process creates good foam slag, uniform decarburization, and reduces nitrogen absorption.
[0045] (3) The goal of the melti...
Embodiment 2
[0053] Example 2: 15B36Cr steel
[0054] 1. The weight percent of the chemical composition of steel is: C0.35 Si0.20 Mn1.35 P0.016 S0.001 B0.0029 Cr0.20Al0.023 Ti0.05 Ti / N=5; the balance is Fe and trace impurities .
Embodiment 3
[0055] Example 3: 15B36Cr steel
[0056] The chemical composition weight percent of the steel is: C0.33 Si0.23 Mn1.35 P0.012 S0.005 B0.0016 Al0.035Ti0.03 Ti / N=4; the balance is Fe and trace impurities.
[0057] The preparation method is the same as in Example 1.
[0058] The furnace numbers of Example 1, Example 2, and Example 3 are T208-4899, T208-4904, and T208-4912 respectively, and the mechanical properties and end hardenability of the rolled materials are shown in Table 1 and Table 2 below.
[0059] Table 1 Mechanical properties of rolled products
[0060] furnace number
Rm(MPa)
tensile strength
ReL(MPa)
Yield Strength
A(%)
Elongation
Z(%)
Shrinkage
Aku(J)
Impact energy
T208-4899
1075 / 1070
940 / 930
16 / 15
52 / 53
110 / 115
T208-4904
1060 / 1065
965 / 965
14 / 15
53 / 52
112 / 97
T208-4912
1055 / 1045 ...
PUM
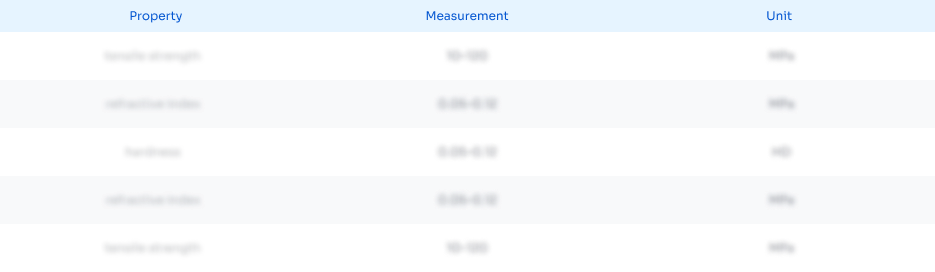
Abstract
Description
Claims
Application Information

- Generate Ideas
- Intellectual Property
- Life Sciences
- Materials
- Tech Scout
- Unparalleled Data Quality
- Higher Quality Content
- 60% Fewer Hallucinations
Browse by: Latest US Patents, China's latest patents, Technical Efficacy Thesaurus, Application Domain, Technology Topic, Popular Technical Reports.
© 2025 PatSnap. All rights reserved.Legal|Privacy policy|Modern Slavery Act Transparency Statement|Sitemap|About US| Contact US: help@patsnap.com