Method for preparing alkali sulphide by using sulfur dye waste gas
A technology of sulfur dyes and alkali sulfide, applied in the direction of alkali metal sulfides/polysulfides, which can solve problems such as human injury and atmospheric environmental pollution, and achieve the effects of less energy consumption, reduced environmental pollution, and convenient operation
- Summary
- Abstract
- Description
- Claims
- Application Information
AI Technical Summary
Problems solved by technology
Method used
Examples
Embodiment 1
[0018] The method for preparing soda sulfide from sulfur dye waste gas, which uses sulfur dye waste gas containing hydrogen sulfide as raw material and makes it enter the bottom of the absorption tower, and feeds it into the tower from the top of the absorption tower through a circulation pump with a flow rate of 150m 3 The sodium hydroxide solution (its weight percentage concentration is 10%) of / h reacts, and the weight ratio of the add-on of sodium hydroxide solution and waste gas is 0.8: 1, and reaction temperature is 60 ℃, absorbs by induced draft fan in the reaction process Exhaust outside the tower (the gas includes some trace gases and water vapor generated during the reaction), and the air volume of the induced draft fan is 11300Nm 3 / h, so that the pressure in the reaction process is-0.12MPa, when the weight percentage concentration of the sodium hydroxide solution at the bottom of the absorption tower is less than 1%, then react to the end, then the reaction solution...
Embodiment 2
[0022] The method for preparing alkali sulfide from sulfur dye waste gas, which uses sulfur dye waste gas containing hydrogen sulfide as raw material and makes it enter the bottom of the absorption tower, and feeds it into the tower from the top of the absorption tower through a circulation pump with a flow rate of 200m 3 The potassium hydroxide solution (its weight percent concentration is 15%) of / h reacts, and the weight ratio of the add-on of potassium hydroxide solution and waste gas is 1: 1, and reaction temperature is 66 ℃, absorbs by induced draft fan in the reaction process Exhaust outside the tower (the gas includes some trace gases and water vapor generated during the reaction), and the air volume of the induced draft fan is 10500Nm 3 / h, so that the pressure in the reaction process is-0.105 MPa, when the concentration by weight of the potassium hydroxide solution at the bottom of the absorption tower is less than 1%, then react to the end, then the reaction solution...
Embodiment 3
[0026] The method for preparing alkali sulfide from sulfur dye waste gas, which uses sulfur dye waste gas containing hydrogen sulfide as raw material and makes it enter the bottom of the absorption tower, and feeds it into the tower from the top of the absorption tower through a circulation pump with a flow rate of 250m 3 The sodium carbonate solution (its weight percentage concentration is 20%) of / h reacts, and the weight ratio of the add-on of sodium carbonate solution and waste gas is 1.2: 1, and temperature of reaction is 72 ℃, by induced draft fan in the reaction process to the outside of absorption tower Exhaust (the gas includes some trace gases and water vapor, CO produced in the reaction process 2 ), the air volume of the induced draft fan is 7700Nm 3 / h, so that the pressure in the reaction process is-0.09MPa, when the weight percent concentration of the sodium carbonate solution at the bottom of the absorption tower is less than 1%, then react to the end, then the ...
PUM
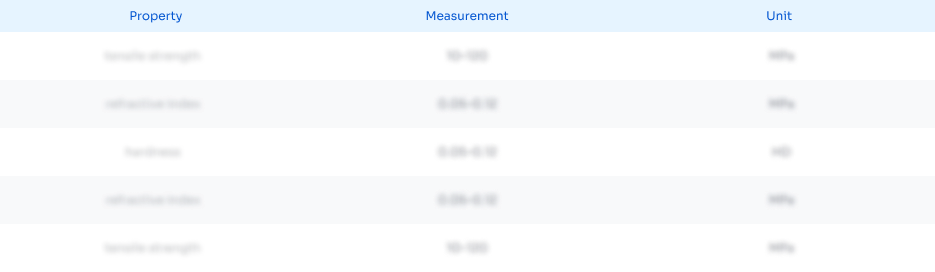
Abstract
Description
Claims
Application Information

- R&D
- Intellectual Property
- Life Sciences
- Materials
- Tech Scout
- Unparalleled Data Quality
- Higher Quality Content
- 60% Fewer Hallucinations
Browse by: Latest US Patents, China's latest patents, Technical Efficacy Thesaurus, Application Domain, Technology Topic, Popular Technical Reports.
© 2025 PatSnap. All rights reserved.Legal|Privacy policy|Modern Slavery Act Transparency Statement|Sitemap|About US| Contact US: help@patsnap.com