Automatic calibration system and automatic calibration method for sonic nozzle
A technology of automatic calibration system and sonic nozzle, applied in jet engine testing, gas turbine engine testing, etc., can solve the problems of time-consuming, labor-intensive, low calibration efficiency, etc., to improve safety, save manpower and time, and eliminate manual operation. Effect
- Summary
- Abstract
- Description
- Claims
- Application Information
AI Technical Summary
Problems solved by technology
Method used
Image
Examples
Embodiment Construction
[0030] Sonic nozzle automatic calibration system such as image 3 As shown, clean high-pressure oxygen is stored in the high-pressure gas storage tank 1 as the system gas source. The high-pressure hand valve 2 is the main switch of the air source, and a pressure sensor 13 is arranged downstream of the high-pressure hand valve 2 to detect the pressure of the air source. Quantitative supply type electronically controlled pressure reducer 14 is arranged upstream of the measured sonic nozzle 8, and its function is to change the upstream high-pressure gas into low-pressure gas and send it to the downstream, and its outlet pressure can be adjusted arbitrarily. A temperature sensor 15 and a pressure sensor 16 are arranged upstream of the sonic nozzle 8 to measure the temperature of oxygen and the inlet pressure of the sonic nozzle. The flow meter 6 is arranged downstream of the measured sonic nozzle 8 to measure the flow. Solenoid valve 9 is a system valve. The signals of the pres...
PUM
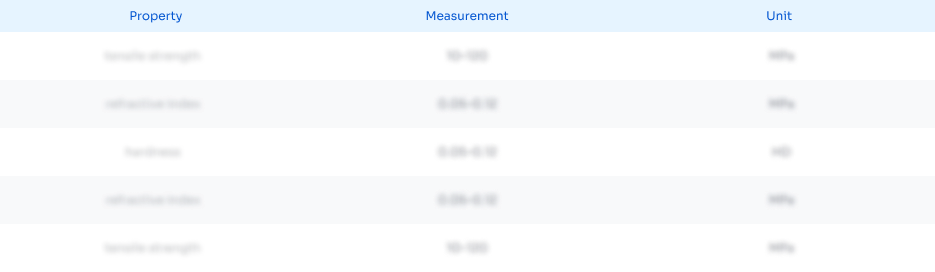
Abstract
Description
Claims
Application Information

- R&D
- Intellectual Property
- Life Sciences
- Materials
- Tech Scout
- Unparalleled Data Quality
- Higher Quality Content
- 60% Fewer Hallucinations
Browse by: Latest US Patents, China's latest patents, Technical Efficacy Thesaurus, Application Domain, Technology Topic, Popular Technical Reports.
© 2025 PatSnap. All rights reserved.Legal|Privacy policy|Modern Slavery Act Transparency Statement|Sitemap|About US| Contact US: help@patsnap.com