Longitudinal and flexural composite transducer type double cylinder-shaped traveling wave ultrasonic motor vibrator
A composite transducer, ultrasonic motor technology, applied in the direction of generator/motor, piezoelectric effect/electrostrictive or magnetostrictive motor, electrical components, etc., can solve the problem of reducing the mechanical output capability and controllability of ultrasonic motor. , the vibration trajectory distortion of the vibrator surface particles, the limitation of the mechanical output capacity of the ultrasonic motor, etc., to achieve the effect of improving the mechanical output capacity and controllability, flexible design, and large torque output
- Summary
- Abstract
- Description
- Claims
- Application Information
AI Technical Summary
Problems solved by technology
Method used
Image
Examples
specific Embodiment approach 1
[0014] Specific implementation mode 1: the following combination Figure 1 ~ Figure 4 To illustrate this embodiment, this embodiment includes a longitudinal-bending composite sandwich transducer 1 and two cylinders 2. The inner wall of the cylinder 2 is evenly distributed along the circumferential direction with a plurality of comb-shaped driving teeth 2-1, and a plurality of comb-shaped The driving tooth 2-1 is parallel to the central axis along the axial direction of the cylinder 2;
[0015] The longitudinal and bending composite sandwich transducer 1 consists of two front end covers 1-1, two first bending vibration piezoelectric ceramic sheets 1-21, two second bending vibration piezoelectric ceramic sheets 1-22, and two first bending vibration piezoelectric ceramic sheets 1-22. One longitudinal vibration piezoelectric ceramic sheet 1-31, two second longitudinal vibration piezoelectric ceramic sheet 1-32, two first electrode sheets 1-41, two second electrode sheets 1-42, two th...
specific Embodiment approach 2
[0021] Embodiment 2: The difference between this embodiment and the first embodiment is that the first bending vibration piezoelectric ceramic sheet 1-21, the second bending vibration piezoelectric ceramic sheet 1-22, the first longitudinal vibration piezoelectric ceramic The cross sections of the sheet 1-31, the second longitudinal vibration piezoelectric ceramic sheet 1-32 and the flange 1-5 are rectangular at the same time. Other components and connection relationships are the same as in the first embodiment.
specific Embodiment approach 3
[0022] Specific embodiment three: This embodiment is different from the first embodiment in that the first bending vibration piezoelectric ceramic sheet 1-21, the second bending vibration piezoelectric ceramic sheet 1-22, the first longitudinal vibration piezoelectric ceramic The cross sections of the sheet 1-31, the second longitudinal vibration piezoelectric ceramic sheet 1-32 and the flange 1-5 are circular at the same time. Other components and connection relationships are the same as in the first embodiment.
PUM
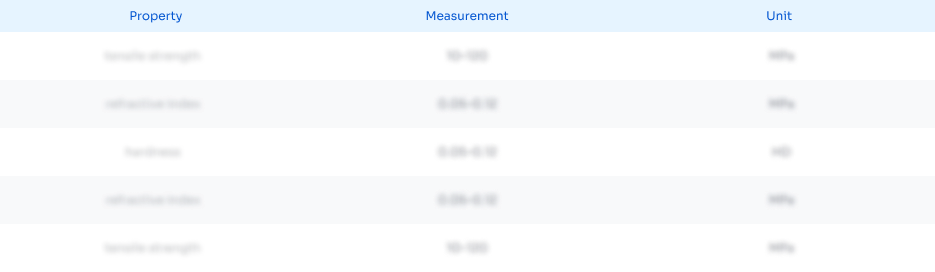
Abstract
Description
Claims
Application Information

- R&D
- Intellectual Property
- Life Sciences
- Materials
- Tech Scout
- Unparalleled Data Quality
- Higher Quality Content
- 60% Fewer Hallucinations
Browse by: Latest US Patents, China's latest patents, Technical Efficacy Thesaurus, Application Domain, Technology Topic, Popular Technical Reports.
© 2025 PatSnap. All rights reserved.Legal|Privacy policy|Modern Slavery Act Transparency Statement|Sitemap|About US| Contact US: help@patsnap.com