Milling cutter manufacturing method
A technology of milling cutters and tool holders, which is applied in the field of manufacturing milling cutters, can solve the problems of repeated use and inability to sharpen, and achieve the effects of reduced component manufacturing costs, high cutting capacity, and reduced machine tool investment requirements
- Summary
- Abstract
- Description
- Claims
- Application Information
AI Technical Summary
Problems solved by technology
Method used
Image
Examples
Embodiment Construction
[0022] The finished milling cutter 1 according to the first embodiment is illustrated in Image 6 and 7 middle. The knife 1 has a cutting head 2 and a coaxial one-piece shank 3 intended to be fastened for rotation about an axis X in a chuck or tool holder of a machine tool.
[0023] The cutting head 2 has a plurality (eg 30) of helical grooves 5 extending from a leading end 6 of the head 2 to a trailing end 7 of the head 2 . Each groove 5 has a tooth 8 comprising a guide face 9 and a back face 10, see figure 1 . The guide surface 9 faces the direction of rotation of the knife 1 in use and has the cutting tip 4 . The cutting tip 4 of each tooth 8 is located on the circumference of a pitch circle with a diameter D, see image 3 . The guide surface 9 has a positive radial rake angle radial rake angle is the angle formed by the inclined guide surface 9 and the radial line Y, see figure 2 , the radial line Y extends from the tool axis X to the tip 4 of the tooth 8 . In...
PUM
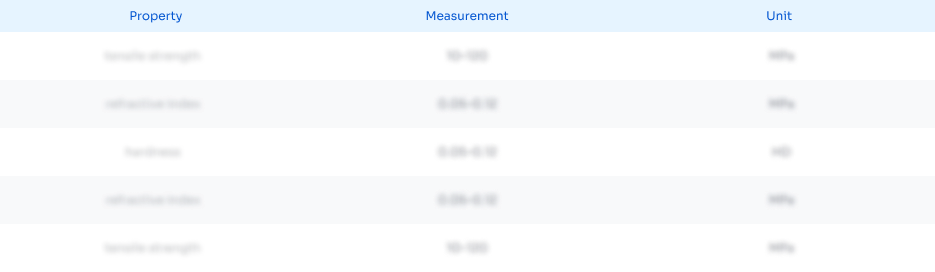
Abstract
Description
Claims
Application Information

- R&D
- Intellectual Property
- Life Sciences
- Materials
- Tech Scout
- Unparalleled Data Quality
- Higher Quality Content
- 60% Fewer Hallucinations
Browse by: Latest US Patents, China's latest patents, Technical Efficacy Thesaurus, Application Domain, Technology Topic, Popular Technical Reports.
© 2025 PatSnap. All rights reserved.Legal|Privacy policy|Modern Slavery Act Transparency Statement|Sitemap|About US| Contact US: help@patsnap.com