Coal blending method for coking chamber coke oven with width of 7.63 meters
A carbonization chamber and coal blending technology, applied in the coking field, can solve the problems of increased coal bulk density, difficulty in maintaining the sustainable development of the coking industry, lack of scientificity, etc., so as to reduce the cost of coal blending and save high-quality coking coal resources. Effect
- Summary
- Abstract
- Description
- Claims
- Application Information
AI Technical Summary
Problems solved by technology
Method used
Examples
Embodiment Construction
[0016] Coal blending method embodiment 1~5 for 7.63 meters coke oven of the present invention, it comprises the following steps:
[0017] Step (1), the step of selecting each single coking coal participating in coal blending;
[0018] Single coking coal includes: coking coal, gas fat coal, 1 / 3 coking coal, lean coal;
[0019] The maximum Gibbs fluidity of the gas-fertilized coal is greater than 60,000 ddpm;
[0020] The dry ash-free base volatile content Vdaf of the 1 / 3 coking coal is between 28% and 37%, the cohesive index G value is greater than 80, and the particle size mosaic index is greater than 72;
[0021] The dry ash-free base volatile content Vdaf of the coking coal is between 20% and 27%, the cohesive index G value is greater than 80, and the proportion of coarse-grained mosaic components is greater than 55%;
[0022] The caking index G value of the lean coal is between 5 and 20;
[0023] Step (2), the step of mixing each single coking coal;
[0024] The weight ...
PUM
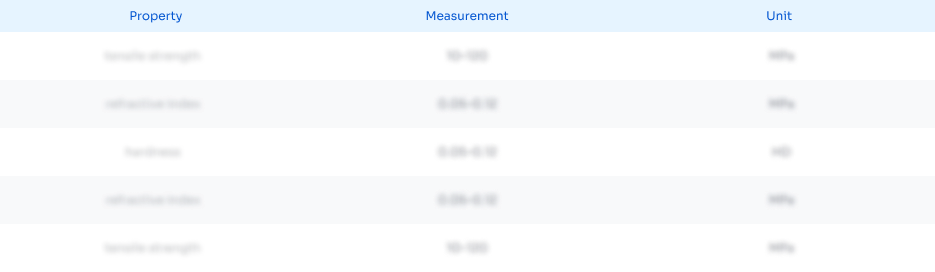
Abstract
Description
Claims
Application Information

- R&D
- Intellectual Property
- Life Sciences
- Materials
- Tech Scout
- Unparalleled Data Quality
- Higher Quality Content
- 60% Fewer Hallucinations
Browse by: Latest US Patents, China's latest patents, Technical Efficacy Thesaurus, Application Domain, Technology Topic, Popular Technical Reports.
© 2025 PatSnap. All rights reserved.Legal|Privacy policy|Modern Slavery Act Transparency Statement|Sitemap|About US| Contact US: help@patsnap.com