Environmental-friendly halogen-free low-smoke flame retardant material for coaxial cable and preparation method thereof
A coaxial cable, low-smoke and flame-retardant technology, applied in the direction of insulated cables, cables, circuits, etc., to achieve good effect, good environmental performance, and less human stimulation
- Summary
- Abstract
- Description
- Claims
- Application Information
AI Technical Summary
Problems solved by technology
Method used
Examples
Embodiment 1
[0009] The formula of each component of the material is: ethylene-vinyl acetate copolymer 24 kg, linear low-density polyethylene 20 kg, flame retardant aluminum hydroxide 75 kg, flame retardant magnesium hydroxide 25 kg, compatibilizer ethylene-vinyl acetate 13 kg of copolymer grafted maleic anhydride copolymer, 1 kg of antioxidant triphenyl phosphite, 1 kg of surfactant vinyl tris (β-methoxyethoxy) silane, 1 kg of lubricant zinc stearate Kilogram.
[0010] The preparation method is as follows: first mix the flame retardant aluminum hydroxide in a high-speed mixer until the temperature reaches 80°C, and then use the surfactant vinyl tris (β-methoxyethoxy) silane as a pre-spraying coating after dehydration. processing, then add each component material and stir in a high-speed mixer for 3 minutes to mix all kinds of materials evenly, and then send the mixture into a twin-screw extruder for processing and granulation. The temperature of each section of the screw is: the feeding s...
Embodiment 2
[0012] The formula of each component of the material is: ethylene-vinyl acetate copolymer 45 kg, linear low-density polyethylene 29 kg, flame retardant aluminum hydroxide 115 kg, flame retardant magnesium hydroxide 30 kg, compatibilizer ethylene-vinyl acetate 16 kg of copolymer grafted maleic anhydride copolymer, 1 kg of antioxidant triphenyl phosphite, 2 kg of surfactant vinyl tris (β-methoxyethoxy) silane, 2 kg of lubricant zinc stearate Kilogram.
[0013] The preparation method is as follows: first mix the flame retardant aluminum hydroxide in a high-speed mixer until the temperature reaches 85°C, and then use the surfactant vinyl tris (β-methoxyethoxy) silane as a pre-spraying coating after dehydration. Processing, then add each component material and stir at high speed in a high-speed mixer for 4 minutes to mix all kinds of materials evenly, and then send the mixture into a twin-screw extruder for processing and granulation. The temperature of each section of the screw is...
Embodiment 3
[0015] The formula of each component of the material is: ethylene-vinyl acetate copolymer 114 kg, linear low density polyethylene 38 kg, flame retardant aluminum hydroxide 150 kg, flame retardant magnesium hydroxide 45 kg, compatibilizer ethylene grafted horse 23 kilograms of anhydride copolymers, 3 kilograms of antioxidant triphenyl phosphites, 3 kilograms of surfactant vinyl tris (β-methoxyethoxy) silanes, 4 kilograms of lubricant zinc stearates.
[0016] The preparation method is as follows: first mix the flame retardant aluminum hydroxide in a high-speed mixer until the temperature reaches 90°C, and then use the surfactant vinyl tris (β-methoxyethoxy) silane as a pre-spraying coating after dehydration. Processing, then add each component material and stir in a high-speed mixer for 5 minutes to mix all kinds of materials evenly, and then send the mixture into a twin-screw extruder for processing and granulation. The temperature of each section of the screw is: feeding sectio...
PUM
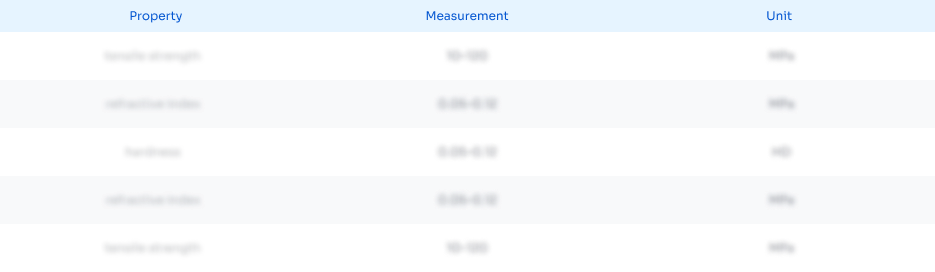
Abstract
Description
Claims
Application Information

- R&D
- Intellectual Property
- Life Sciences
- Materials
- Tech Scout
- Unparalleled Data Quality
- Higher Quality Content
- 60% Fewer Hallucinations
Browse by: Latest US Patents, China's latest patents, Technical Efficacy Thesaurus, Application Domain, Technology Topic, Popular Technical Reports.
© 2025 PatSnap. All rights reserved.Legal|Privacy policy|Modern Slavery Act Transparency Statement|Sitemap|About US| Contact US: help@patsnap.com