Method for producing low alkali cement by using high alkali raw materials
A low-alkali cement and raw material technology, applied in the direction of alkali metal chloride, etc., can solve the problems of insufficient low-alkali raw materials, low-alkali cement can not meet the needs of low-alkali cement, etc.
- Summary
- Abstract
- Description
- Claims
- Application Information
AI Technical Summary
Problems solved by technology
Method used
Image
Examples
Embodiment 1
[0041] The production line of a cement plant has a daily output of 3,000 tons of cement clinker (consumption of about 3,000 tons of hot raw materials and about 4,500 tons of raw materials) (using a dry-process cement rotary kiln with a suspension preheater and a precalciner kiln). See Table 1 and Table 2 below for the element content of raw materials and cement products before adding Cl element.
[0042] Table 1 The content of each element in the hot raw meal entering the kiln (%)
[0043] SiO 2
[0044] Content of each element in table 2 cement (%)
[0045] SiO 2
[0046] Under this condition, the alkali equivalent of the cement product is 0.14%+0.658×1.16%=0.90328%, which is greater than 0.60%, which does not meet the requirements of low-alkali cement.
[0047] Calculate the amount of added chlorine should be greater than 14.7 tons, less than 38.97 tons, see the following formula (4) and (5). Add 30 tons of PCB to the kiln system through the kiln he...
Embodiment 2
[0054] The production line of a cement factory produces 3,000 tons of cement clinker per day (dry cement rotary kiln with suspension preheater and precalciner kiln). 5.
[0055] Table 4 The content of each element in the hot raw meal entering the kiln (%)
[0056] SiO 2
[0057] Content of each element in table 5 cement (%)
[0058] SiO 2
[0059] Calculate the amount of added chlorine should be greater than 19.07 tons, less than 41.24 tons see the following formula (6) and (7).
[0060] Add 7.5 tons of fly ash per hour to the kiln system through the kiln head, with a Cl content of 12%. And 10% of the air volume of the system is drawn out by the device provided by the invention, the hot flue gas first passes through the mixing chamber to cool down and then enters the heat exchanger, heats the heat transfer oil in the heat exchanger, and the heat transfer oil provides heat for other heat-requiring equipment. The flue gas coming out of the heat exchang...
PUM
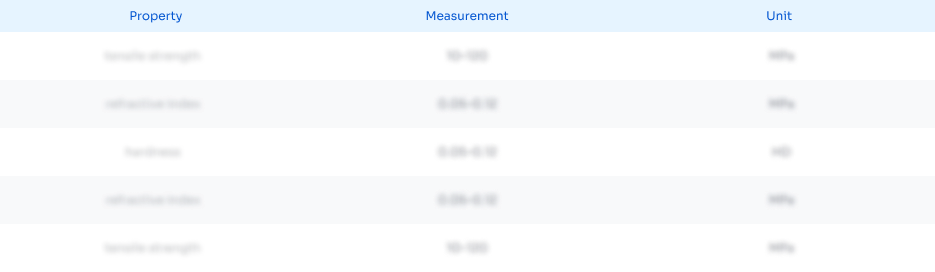
Abstract
Description
Claims
Application Information

- R&D
- Intellectual Property
- Life Sciences
- Materials
- Tech Scout
- Unparalleled Data Quality
- Higher Quality Content
- 60% Fewer Hallucinations
Browse by: Latest US Patents, China's latest patents, Technical Efficacy Thesaurus, Application Domain, Technology Topic, Popular Technical Reports.
© 2025 PatSnap. All rights reserved.Legal|Privacy policy|Modern Slavery Act Transparency Statement|Sitemap|About US| Contact US: help@patsnap.com