Method for manufacturing printed wiring board
A technology for printed circuit boards and manufacturing methods, which is applied in the fields of printed circuit manufacturing, multilayer circuit manufacturing, printed circuit, etc., can solve problems such as increased workload and troublesome manufacturing of printed circuit boards, and achieve a sudden reduction in the number of processes, quick and easy results
- Summary
- Abstract
- Description
- Claims
- Application Information
AI Technical Summary
Problems solved by technology
Method used
Image
Examples
Embodiment approach
[0067] Next, an example of the following embodiments of the present invention will be described. In this embodiment, a method of manufacturing a printed wiring board having through holes will be described with reference to the drawings.
[0068] In the manufacturing method of the printed wiring board of the present embodiment, first, as Figure 6 As shown, prepare the existing copper clad laminate 4 . Next, since in this embodiment mode is formed as Figure 14 The steps before the shown through-hole 17 are the same as the conventional steps, and therefore description thereof will be omitted.
[0069] Such as Figure 14 As shown, it is assumed that the via hole 17 is formed through a via hole forming step.
[0070] Such as figure 1 As shown, in this embodiment, the etching step is provided before or after the via hole forming step. In this etching step, copper foil 15 is removed by etching. Then, in the degreasing process, the whole is degreased. Thus, if Figure 5 As ...
PUM
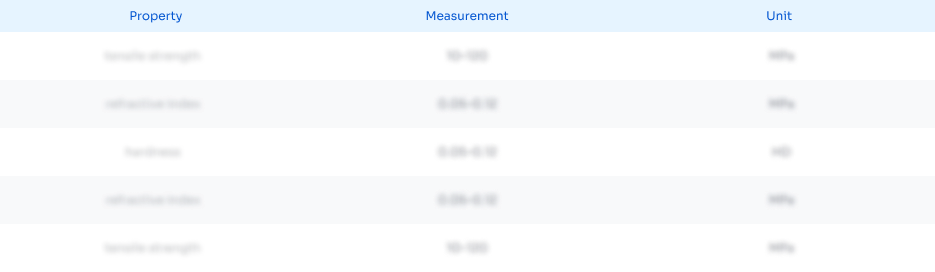
Abstract
Description
Claims
Application Information

- R&D
- Intellectual Property
- Life Sciences
- Materials
- Tech Scout
- Unparalleled Data Quality
- Higher Quality Content
- 60% Fewer Hallucinations
Browse by: Latest US Patents, China's latest patents, Technical Efficacy Thesaurus, Application Domain, Technology Topic, Popular Technical Reports.
© 2025 PatSnap. All rights reserved.Legal|Privacy policy|Modern Slavery Act Transparency Statement|Sitemap|About US| Contact US: help@patsnap.com