Process for applying hydrogen to deoxygenation of liquid steel
A liquid steel and process technology, applied in the field of molten steel deoxidation process, can solve the problem that the pollution of deoxidation products cannot be completely avoided, so as to improve the cleanliness of molten steel and the quality of steel, reduce the pollution of molten steel, and reduce the effect of obstruction
- Summary
- Abstract
- Description
- Claims
- Application Information
AI Technical Summary
Problems solved by technology
Method used
Examples
Embodiment 1
[0013] A process in which hydrogen is used to deoxidize molten steel. Low-carbon steel is produced in a 200t converter, and H 2 Blowing into molten steel for deoxidation, blowing into molten steel for deoxidation is to blow H 2 Deoxidation is carried out by blowing air bricks into molten steel from the bottom of the top-bottom combined blowing converter. h 2 The flow rate is 300~1800m 3 / h, the pressure is 0.5~1.5MPa, and the time for blowing into molten steel is 10~30min.
[0014] At the end of hydrogen blowing and deoxygenation in the converter, the hydrogen dissolved in the steel is removed by blowing argon and vacuum treatment.
Embodiment 2
[0016] A process in which hydrogen is used to deoxidize molten steel. Low-carbon steel is produced in a 300t converter, and Ar-H 2 The mixed gas is blown into molten steel for deoxidation, Ar-H 2 The mixed gas flow rate is 800~3000m 3 / h, the pressure is 0.5~1.0MPa, and the time for blowing the mixed gas into the molten steel is 5~20min.
[0017] At the end of hydrogen blowing and deoxygenation in the converter, the hydrogen dissolved in the steel is removed by blowing argon and vacuum treatment.
[0018] In this embodiment: blowing into the molten steel for deoxidation is to use Ar-H 2 The mixed gas is blown into the molten steel from the bottom of the top-bottom combined blowing converter through the breathable brick for deoxidation; in the Ar-H 2 In the mixed gas, the volume content of Ar is 10-50%, H 2 The volume content is 50-90%.
Embodiment 3
[0020] A process in which hydrogen is used to deoxidize molten steel. In the production of aluminum killed steel, H 2 Blowing into unalloyed molten steel for deoxidation, blowing into molten steel for deoxidation is to blow H 2 Blow into molten steel through the breathable brick at the bottom for deoxidation. h 2 The flow rate is 40~200m 3 / h, the pressure is 0.5~1.5MPa, H 2 The time for blowing into molten steel is 10-30 minutes. At the end of hydrogen blowing and deoxidation of the ladle, the hydrogen dissolved in the steel is removed by argon blowing and vacuum treatment.
PUM
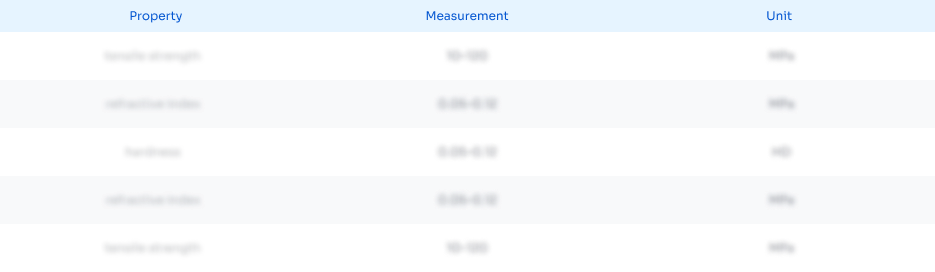
Abstract
Description
Claims
Application Information

- R&D
- Intellectual Property
- Life Sciences
- Materials
- Tech Scout
- Unparalleled Data Quality
- Higher Quality Content
- 60% Fewer Hallucinations
Browse by: Latest US Patents, China's latest patents, Technical Efficacy Thesaurus, Application Domain, Technology Topic, Popular Technical Reports.
© 2025 PatSnap. All rights reserved.Legal|Privacy policy|Modern Slavery Act Transparency Statement|Sitemap|About US| Contact US: help@patsnap.com