Adjustable glow monitoring system of glow equipment
A monitoring system and adjustable technology, applied in control/regulation systems, light control, climate sustainability, etc., can solve problems such as unclean silicon etching, interference with monitoring system signals, product abnormalities, etc., to achieve monitoring reliability Enhanced, stabilized reaction conditions, less prone to misoperation
- Summary
- Abstract
- Description
- Claims
- Application Information
AI Technical Summary
Problems solved by technology
Method used
Image
Examples
Embodiment 1
[0025] like figure 1 As shown, a glow device adjustable glow monitoring system of the present invention includes a photosensitive sensor for monitoring glow intensity, a connecting cable and a controller 3, the controller 3 adopts a programmable logic controller (PLC), and the photosensitive sensor includes The switch quantity photosensitive sensor 11 and the analog quantity photosensitive sensor 12, the programmable controller is equipped with a warning device connected with its power, the warning device adopts the buzzer 6 and the indicator light 7 which shows different alarm levels with different color lamp tubes, the switch quantity The photosensitive sensor 11 has a control circuit for setting the glow intensity, and the set intensity is regulated by a regulator in the control circuit. The switching value photosensitive sensor 11 and the analog quantity photosensitive sensor 12 are respectively connected to the programmable The controller; the off-quantity photosensitive ...
Embodiment 2
[0032] The difference between this embodiment and Embodiment 1 is that the photosensitive sensor only adopts the switching value photosensitive sensor, the distance between the switching value photosensitive sensor and the side wall of the glow generating cavity is 5cm, and the controller adopts an industrial computer. When the glow intensity monitored by the photosensitive sensor rises or falls to the set value of the glow intensity, the switch value photosensitive sensor sends a switch signal to the industrial computer, and the industrial computer receives the signal, and realizes the buzzing by calculating the pre-programmed program indicator and indicator light.
Embodiment 3
[0034] The difference between this embodiment and Embodiment 1 is that the photosensitive sensor only uses an analog photosensitive sensor, the distance between the analog photosensitive sensor and the side wall of the glow generating cavity is 20 cm, and the analog photosensitive sensor controls the glow intensity. The analog quantity is converted and the converted signal is sent to the programmable controller. The programmable controller converts the converted signal into the actual power of the glow power supply through the corresponding relationship between the converted signal and the glow power supply obtained in advance, that is, the glow power supply Power data recording and control of the output of the glow power supply to realize the adjustment of the glow intensity.
PUM
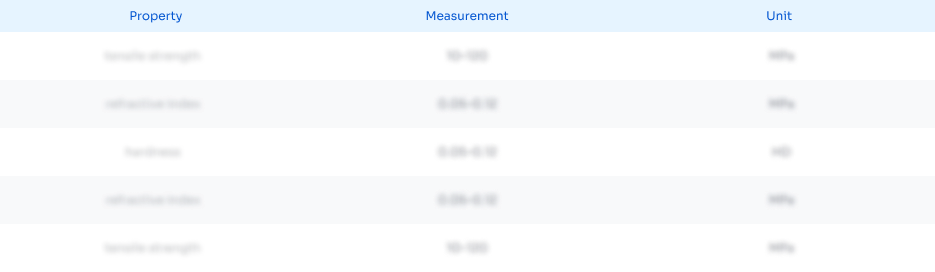
Abstract
Description
Claims
Application Information

- R&D Engineer
- R&D Manager
- IP Professional
- Industry Leading Data Capabilities
- Powerful AI technology
- Patent DNA Extraction
Browse by: Latest US Patents, China's latest patents, Technical Efficacy Thesaurus, Application Domain, Technology Topic, Popular Technical Reports.
© 2024 PatSnap. All rights reserved.Legal|Privacy policy|Modern Slavery Act Transparency Statement|Sitemap|About US| Contact US: help@patsnap.com