Rolling technical skill of hot strip rough rolling process
A technology of hot-rolled strip steel and process technology, applied in metal rolling, metal rolling, manufacturing tools, etc., can solve the problems of large temperature drop and many rolling passes in the rough rolling area of the strip, and achieve production efficiency High, short process, low investment effect
- Summary
- Abstract
- Description
- Claims
- Application Information
AI Technical Summary
Problems solved by technology
Method used
Image
Examples
Embodiment Construction
[0019] With reference to accompanying drawing, concrete implementation of the present invention is described further:
[0020] The continuous casting slab with a thickness of 135-250 mm is heated to the prescribed temperature in the heating (homogeneous) furnace 1, and then enters the rough rolling high-pressure water descaling box 2 through the roller table to remove the scale, and then enters the No.1 tandem Reversible four-roll roughing mill 3 and No.2 tandem reversible four-roll roughing mill 4 The roughing unit composed of two tandem arrangements performs reversible rolling for 3 to 5 passes, and rolls to a certain thickness (30 to 60mm) After the intermediate billet is insulated by the heat preservation cover 5 or the hot coil box 6, the head and tail are cut by the flying shear 7, and the finished rolling high-pressure water descaling box 8 removes the regenerated iron scale, it is rolled by the finishing rolling unit 9 composed of 5 to 7 irreversible rolling mills. The...
PUM
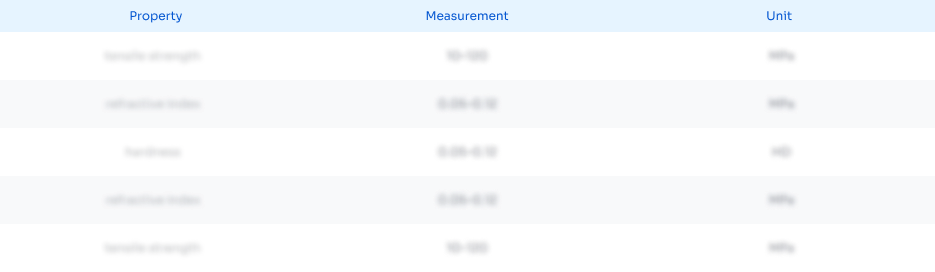
Abstract
Description
Claims
Application Information

- Generate Ideas
- Intellectual Property
- Life Sciences
- Materials
- Tech Scout
- Unparalleled Data Quality
- Higher Quality Content
- 60% Fewer Hallucinations
Browse by: Latest US Patents, China's latest patents, Technical Efficacy Thesaurus, Application Domain, Technology Topic, Popular Technical Reports.
© 2025 PatSnap. All rights reserved.Legal|Privacy policy|Modern Slavery Act Transparency Statement|Sitemap|About US| Contact US: help@patsnap.com