Method for hot dip galvanizing of nickel-vanadium alloy plating coat on rolled steel
A technology of hot-dip galvanizing and nickel-vanadium alloy, applied in hot-dip galvanizing process, metal material coating process, coating, etc., can solve the problems of little improvement in corrosion resistance and thinning coating, and achieve improved corrosion resistance Performance, reduced weight gain, and improved antioxidant properties
- Summary
- Abstract
- Description
- Claims
- Application Information
AI Technical Summary
Problems solved by technology
Method used
Image
Examples
Embodiment 1
[0022] The steel used for galvanizing is a steel plate containing 0.10% Si, the size specification is 50mm×40mm×3mm, and the chemical composition is shown in Table 1 below. Its method for hot-dip galvanizing nickel-vanadium alloy coating on steel comprises the following steps and process conditions:
[0023] (1) Binary master alloy refining: Weigh nickel and zinc, vanadium and zinc according to weight ratio, put nickel and zinc in one graphite crucible, put vanadium and zinc in another graphite crucible, and refine them separately. Wherein, the nickel weight content in the zinc-nickel binary master alloy raw material is 2%, the smelting temperature of the zinc-nickel master alloy is 600 ℃, and is kept at 600 ℃ for 3 hours; the vanadium weight content in the zinc-vanadium binary master alloy raw material is 1.6%, the smelting temperature of the zinc-vanadium master alloy is 720°C, and it is kept at this temperature for 3.5 hours. After heat preservation, the master alloy liqui...
Embodiment 2
[0040] The steel used for galvanizing is Q235 containing (0.22% Si) steel plate, the size specification is 50mm×40mm×3mm, the method adopted includes the following steps and process conditions:
[0041] (1) Binary master alloy refining: Weigh nickel and zinc, vanadium and zinc according to weight ratio, put nickel and zinc in one graphite crucible, put vanadium and zinc in another graphite crucible, and refine them separately. Among them, the nickel content in the zinc-nickel binary master alloy raw material is 2.4%, the smelting temperature of the zinc-nickel master alloy is 610°C, and it is kept at this temperature for 3.5 hours; the vanadium content in the zinc-vanadium binary master alloy raw material is 1% , the melting temperature of the zinc-vanadium master alloy is 710°C, and it is kept at this temperature for 4 hours. After heat preservation, the master alloy liquid is stirred, left still and the ash on the surface of the alloy liquid is removed, and then poured into ...
Embodiment 3
[0047] The steel used for galvanizing is Q235 (containing 0.22% Si) steel plate, and the size specification is 50mm×40mm×3mm. The method adopted includes the following steps and process conditions:
[0048] (1) Binary master alloy refining: Weigh nickel and zinc, vanadium and zinc according to weight ratio, put nickel and zinc in one graphite crucible, put vanadium and zinc in another graphite crucible, and refine them separately. Among them: the nickel content in the zinc-nickel binary master alloy raw material is 3%, the smelting temperature of the zinc-nickel master alloy is 620°C, and it is kept at this temperature for 4 hours; the vanadium content in the zinc-vanadium binary master alloy raw material is 2% , the melting temperature of the zinc-vanadium master alloy is 730°C, and it is kept at this temperature for 3 hours. After heat preservation, the master alloy liquid is stirred, left still and the ash on the surface of the alloy liquid is removed, and then poured into ...
PUM
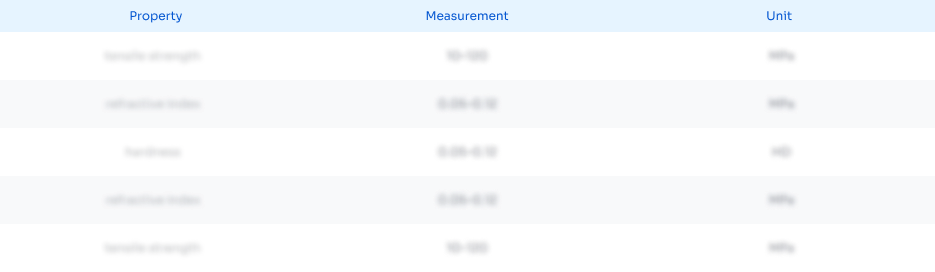
Abstract
Description
Claims
Application Information

- R&D Engineer
- R&D Manager
- IP Professional
- Industry Leading Data Capabilities
- Powerful AI technology
- Patent DNA Extraction
Browse by: Latest US Patents, China's latest patents, Technical Efficacy Thesaurus, Application Domain, Technology Topic, Popular Technical Reports.
© 2024 PatSnap. All rights reserved.Legal|Privacy policy|Modern Slavery Act Transparency Statement|Sitemap|About US| Contact US: help@patsnap.com