Method for obtaining nickel zirconium alloy plating by performing hot-dip galvanizing of rolled steel
A technology for hot-dip galvanizing and zirconium alloys, which is applied to the field of hot-dip galvanizing alloys for steel, can solve the problem of little improvement in corrosion resistance, and achieve the effects of easy composition, delaying the formation of white rust, and simple process
- Summary
- Abstract
- Description
- Claims
- Application Information
AI Technical Summary
Problems solved by technology
Method used
Image
Examples
Embodiment 1
[0058] The steel used for galvanizing is a steel plate containing 0.10% Si, the size specification is 50mm×40mm×3mm, and the chemical composition is shown in Table 1 below. The method adopted comprises the following steps and process conditions:
[0059] (1) Binary master alloy refining: Weigh nickel and zinc, zirconium and zinc according to weight ratio, put nickel and zinc in a graphite crucible, put zirconium and zinc in another graphite crucible, and refine them separately. Among them, the nickel weight content in the zinc-nickel binary master alloy is 2%, the melting temperature of the zinc-nickel master alloy is 600°C, and the holding time is 3 hours; the zirconium weight content in the zinc-zirconium binary master alloy is 2%, the zinc-zirconium master alloy The melting temperature of the master alloy is 720°C, and the holding time is 3.5 hours. After the alloy liquid of zinc-nickel binary master alloy and zinc-zirconium master alloy is kept warm, it is stirred, left s...
Embodiment 2
[0073] The steel used for galvanizing is Q235 containing (0.22% Si) steel plate, the size specification is 50mm×40mm×3mm, the method adopted includes the following steps and process conditions:
[0074] (1) Binary master alloy refining: Weigh nickel and zinc, zirconium and zinc according to weight ratio, put nickel and zinc in a graphite crucible, put zirconium and zinc in another graphite crucible, and refine them separately. Among them, the nickel content in the zinc-nickel binary master alloy is 2.4%, the melting temperature of the zinc-nickel master alloy is 610°C, and the holding time is 3.5 hours; the vanadium content in the zinc-vanadium binary master alloy is 1%, and the zinc-zirconium master alloy The smelting temperature is 710°C, and the holding time is 4 hours. After the alloy liquid of zinc-nickel binary master alloy and zinc-zirconium master alloy is kept warm, it is stirred, left still and the ash on the surface of the alloy liquid is removed, and then cast into...
Embodiment 3
[0079] The steel used for galvanizing is Q235 (containing 0.22% Si) steel plate, and the size specification is 50mm×40mm×3mm. The method adopted includes the following steps and process conditions:
[0080] (1) Binary master alloy refining: Weigh nickel and zinc, zirconium and zinc according to weight ratio, put nickel and zinc in a graphite crucible, put zirconium and zinc in another graphite crucible, and refine them separately. Among them: the nickel content in the zinc-nickel binary master alloy is 3%, the melting temperature of the zinc-nickel master alloy is 620°C, and the holding time is 4 hours; the vanadium content in the zinc-zirconium binary master alloy is 2%, and the zinc-zirconium master alloy The smelting temperature is 730°C, and the holding time is 3 hours. After the alloy liquid of zinc-nickel binary master alloy and zinc-zirconium master alloy is kept warm, it is stirred, left still and the ash on the surface of the alloy liquid is removed, and then cast int...
PUM
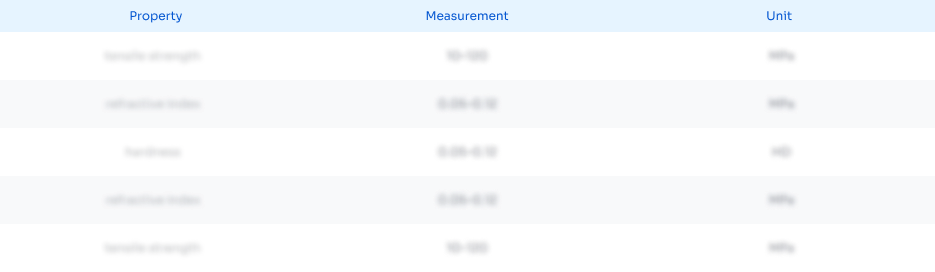
Abstract
Description
Claims
Application Information

- R&D Engineer
- R&D Manager
- IP Professional
- Industry Leading Data Capabilities
- Powerful AI technology
- Patent DNA Extraction
Browse by: Latest US Patents, China's latest patents, Technical Efficacy Thesaurus, Application Domain, Technology Topic, Popular Technical Reports.
© 2024 PatSnap. All rights reserved.Legal|Privacy policy|Modern Slavery Act Transparency Statement|Sitemap|About US| Contact US: help@patsnap.com