Laser welding method for butting two pieces of metal sheets
A thin metal plate and laser welding technology, which is applied in laser welding equipment, welding equipment, metal processing, etc., can solve the problems of welding penetration and leakage, affecting the strength of the weld, and burning of the base material, so as to eliminate weld pit cracks and improve Welding quality, effect of eliminating influence
- Summary
- Abstract
- Description
- Claims
- Application Information
AI Technical Summary
Problems solved by technology
Method used
Image
Examples
Embodiment Construction
[0031] Hereinafter, the present invention will be further described in detail through specific embodiments in conjunction with the drawings.
[0032] A laser welding method for butting two thin metal plates, including the following steps:
[0033] The first step: determine an appropriate spot size according to the thin metal plate, select the corresponding laser welding equipment according to the spot size, and determine the welding height.
[0034] If there is no special requirement when welding with the present invention, the laser spot should be as small as possible to prevent excessive thermal deformation caused by a large heated area during welding, but the spot should completely cover the butt joint of the two thin metal plates and leave a small margin such as three About one part. Specifically, the laser spot diameter ≥ the thickness of the thin metal plate / the aspect ratio of the pulsed laser. Generally, after pulsed laser welding of thin metal plates such as stainless ste...
PUM
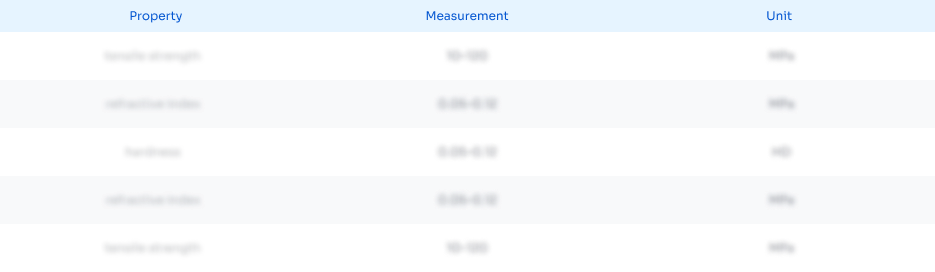
Abstract
Description
Claims
Application Information

- R&D Engineer
- R&D Manager
- IP Professional
- Industry Leading Data Capabilities
- Powerful AI technology
- Patent DNA Extraction
Browse by: Latest US Patents, China's latest patents, Technical Efficacy Thesaurus, Application Domain, Technology Topic, Popular Technical Reports.
© 2024 PatSnap. All rights reserved.Legal|Privacy policy|Modern Slavery Act Transparency Statement|Sitemap|About US| Contact US: help@patsnap.com