Method and device for measuring electric hysteresis loop and strain loop of ferroelectric material simultaneously
A technology of hysteresis loops and ferroelectric materials, applied in measuring devices, measuring electrical variables, electromagnetic measuring devices, etc., can solve the problems of many accessories, inconvenient use, long measurement time, etc., and achieve the effect of high measurement accuracy
- Summary
- Abstract
- Description
- Claims
- Application Information
AI Technical Summary
Problems solved by technology
Method used
Image
Examples
Embodiment 1
[0041] The test sample uses PZT-5 (Institute of Acoustics, Chinese Academy of Sciences) ceramic sample, sample thickness d=1mm, electrode area S=0.7854cm 2 , the experiment uses a triangular wave with a frequency of 0.2Hz and 2 cycles as the measurement signal. During operation, lower the LVDT so that the probe is in contact with the surface of the sample electrode. Observe the input signal display waveform on the interface, and confirm that the LVDT signal Displacement (green waveform) is within the linear range.
[0042] Click the Start button on the interface to start the measurement. After the end, the hysteresis loop and strain loop of the second cycle are obtained. The interface displays the values of spontaneous polarization Ps, remanent polarization Pr, and coercive field Ec at the same time. The data Files and loop diagrams are automatically saved with user name, sample name, test field strength and other parameters as file names. Measurement results from Figure...
Embodiment 2
[0052] The test sample uses PZT-5 (Institute of Acoustics, Chinese Academy of Sciences) ceramic sample, sample thickness d=1mm, electrode area S=0.7854cm 2 , the experiment uses a frequency of 0.2Hz, 2 cycles of the triangular wave as the polarization field strength. Before measurement, click the Polarization Centering and Strain Centering buttons on the interface to perform automatic zero compensation on the loop, and click the Strain Filter button on the interface to filter the strain loop. Figure 7 It is the measurement result after compensating the electric hysteresis loop and strain loop by computer. The interface shows Ps=33.9219μC / cm2, Pr=31.554μC / cm2, Ec=1.11417kV / mm, and draws two loops and test signals in real time (such as Figure 7 a. Figure 7 shown in b).
PUM
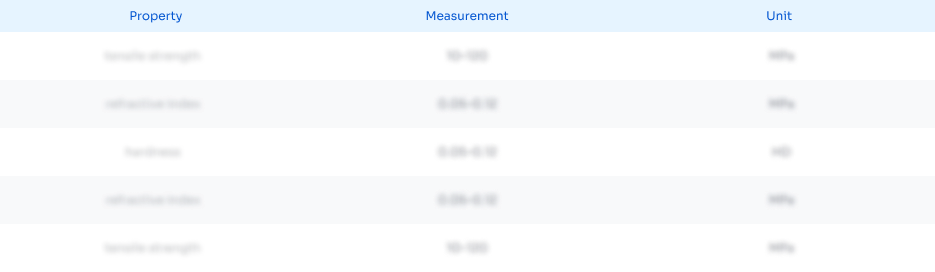
Abstract
Description
Claims
Application Information

- Generate Ideas
- Intellectual Property
- Life Sciences
- Materials
- Tech Scout
- Unparalleled Data Quality
- Higher Quality Content
- 60% Fewer Hallucinations
Browse by: Latest US Patents, China's latest patents, Technical Efficacy Thesaurus, Application Domain, Technology Topic, Popular Technical Reports.
© 2025 PatSnap. All rights reserved.Legal|Privacy policy|Modern Slavery Act Transparency Statement|Sitemap|About US| Contact US: help@patsnap.com