Large capacity temperature equalizing energy saving roller kiln
A large-capacity, roller kiln technology, applied in the field of roller kiln, can solve problems such as unsatisfactory effects, achieve the effects of improving heat exchange effect and cooling efficiency, increasing heat capacity, and reducing temperature difference
- Summary
- Abstract
- Description
- Claims
- Application Information
AI Technical Summary
Problems solved by technology
Method used
Image
Examples
Embodiment 2
[0032] The structure of the ultra-wide kiln body 1 of embodiment 2 is basically the same as that of embodiment 1, the difference is:
[0033] The upper tube panel pipeline group 11 and the lower tube panel pipeline group 12 can also be installed along the kiln width direction. The upper tube panel pipelines 49, 50 are installed above the roller bar 27, and the lower tube panel pipelines 51, 52 are installed below the roller bar 27. The upper tube panel pipelines 49 and 50 and the lower tube panel pipelines 51 and 52 are all directly fixed on the ultra-wide kiln body 1 .
PUM
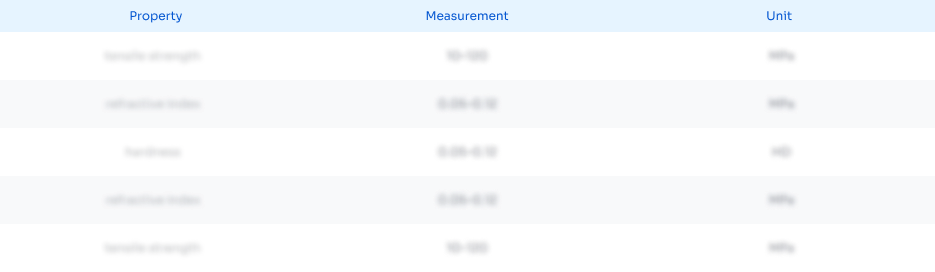
Abstract
Description
Claims
Application Information

- Generate Ideas
- Intellectual Property
- Life Sciences
- Materials
- Tech Scout
- Unparalleled Data Quality
- Higher Quality Content
- 60% Fewer Hallucinations
Browse by: Latest US Patents, China's latest patents, Technical Efficacy Thesaurus, Application Domain, Technology Topic, Popular Technical Reports.
© 2025 PatSnap. All rights reserved.Legal|Privacy policy|Modern Slavery Act Transparency Statement|Sitemap|About US| Contact US: help@patsnap.com