Manufacturing method for burning light burning magnesite powder by tunnel kiln
A light-burned magnesium powder and production method technology, which is applied in the production field of firing light-burned magnesium powder in a tunnel kiln, can solve the problem of large temperature difference between the upper and lower sections of the tunnel kiln, over-burning of the upper part and under-burning of the lower part, prolonging the firing time, Waste of energy and other issues, to achieve the effect of improving temperature uniformity and heat transfer conditions, shortening high-temperature calcination time, and reducing fuel consumption
- Summary
- Abstract
- Description
- Claims
- Application Information
AI Technical Summary
Problems solved by technology
Method used
Image
Examples
Embodiment 1
[0038] Take 900 kg of magnesite flotation tailings (particle size ≤ 0.15mm) and 100 kg of lightly burned magnesium powder (particle size ≤ 0.074mm) according to the mass method, mix them evenly in the kneader, and machine them into bricks. The bricks are: Length×width×thickness=230×130×30mm, dried at 180-200° C. for 6 hours, and loaded on the tunnel kiln car platform 6 with longitudinal flame channels.
[0039] Such as figure 1 As shown, there is a layer of permeable bricks 5 on the table of the kiln car 6, and brick stacks 7 are stacked on the fire bricks. The channel 4 in the stack should be straight in the vertical direction, and the gap 1 formed between the brick stack 7 and the kiln side wall 2 and the top wall 8 is an outer channel.
[0040] The sum of the cross-sectional area of the longitudinal channels of the brick stacks is 0.58 square meters, and the cross-sectional area of the kiln cavity is 1.87 square meters; the sum of the cross-sectional areas of the outer...
Embodiment 2
[0045] Take 800 kg of magnesite flotation tailings (particle size ≤ 0.15mm) according to the mass method, mix them evenly in the kneader, and machine them into adobe. The adobe is: length × width × thickness = 250 × 130 × 50mm. Dried at 130°C for 12 hours, loaded on tunnel kiln cars with longitudinal flame passages, and the longitudinal passages between brick stacks should be straight. Such as figure 1 As shown, there is a layer of permeable bricks 5 on the table of the kiln car 6, and brick stacks 7 are stacked on the fire bricks. The channel 4 in the stack should be straight in the vertical direction, and the gap 1 formed between the brick stack 7 and the kiln side wall 2 and the top wall 8 is an outer channel.
[0046] The sum of the cross-sectional area of the longitudinal channels of the brick stacks is 0.74 square meters, and the cross-sectional area of the kiln cavity is 1.87 square meters; the sum of the cross-sectional areas of the outer channels of the brick sta...
Embodiment 3
[0051] According to the mass method, take 800 kg of magnesite flotation tailings (particle size ≤ 0.15mm) and mix them evenly in the kneader, and then machine them into a brick. Dried at 180°C for 12 hours, loaded on tunnel kiln cars with longitudinal flame passages, and the longitudinal passages between brick stacks should be straight.
[0052] Such as figure 1 As shown, there is a layer of permeable bricks 5 on the table of the kiln car 6, and brick stacks 7 are stacked on the fire bricks. The channel 4 in the stack should be straight in the vertical direction, and the gap 1 formed between the brick stack 7 and the kiln side wall 2 and the top wall 8 is an outer channel.
[0053] The sum of the cross-sectional area of the longitudinal channels of the brick stacks is 0.66 square meters, and the cross-sectional area of the kiln cavity is 1.87 square meters; the sum of the cross-sectional areas of the outer channels of the brick stacks is 0.37 square meters; The sum of th...
PUM
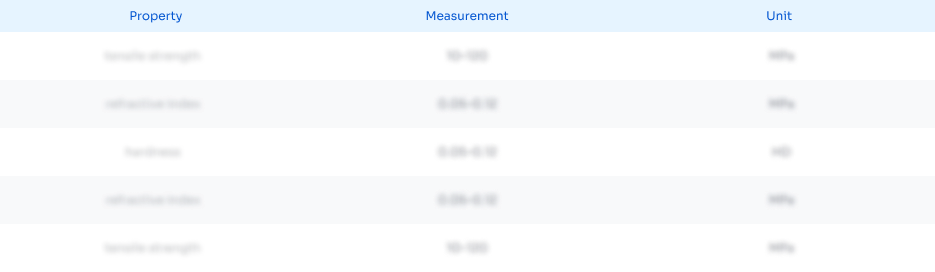
Abstract
Description
Claims
Application Information

- R&D
- Intellectual Property
- Life Sciences
- Materials
- Tech Scout
- Unparalleled Data Quality
- Higher Quality Content
- 60% Fewer Hallucinations
Browse by: Latest US Patents, China's latest patents, Technical Efficacy Thesaurus, Application Domain, Technology Topic, Popular Technical Reports.
© 2025 PatSnap. All rights reserved.Legal|Privacy policy|Modern Slavery Act Transparency Statement|Sitemap|About US| Contact US: help@patsnap.com