Method for measuring defect thickness in carbon/silicon carbide composite material
A composite material, internal defect technology, applied in the measurement device, the use of wave/particle radiation, the preparation of test samples, etc., can solve the problem that the shape of the defect cannot be captured at one time, and the efficiency is low, so as to facilitate digital analysis and improve detection efficiency. Effect
- Summary
- Abstract
- Description
- Claims
- Application Information
AI Technical Summary
Problems solved by technology
Method used
Image
Examples
Embodiment 1
[0054] Example 1: Designing and preparing a needle-punched C / SiC material standard sample containing blind via defects with varying thickness.
[0055] refer to Figure 1~4 , the specific steps are:
[0056] 1. Choose carbon fiber needle-punched felt as the prefabricated body, and cut it into a thin plate shape with a size of 240mm*135mm*8mm. The pyrolytic carbon interface layer was deposited on the preform, and the process conditions were: deposition temperature: 800°C, pressure 0.2Kpa, propylene flow rate 35ml / min, Ar gas flow rate 250ml / min, and deposition time 60h.
[0057] The silicon carbide substrate was deposited on the needle felt with the pyrolytic carbon interface layer deposited, the process conditions were: deposition temperature 800 °C, pressure 4KPa, H 2 Gas flow 150ml / min, Ar gas flow 250ml / min, trichloromethylsilane temperature 35°C, H 2 The molar mass ratio to MTS is 1:12, and the deposition time is 240h. Finally, a needle-punched C / SiC composite board is...
Embodiment 2
[0065] Embodiment 2: Design a high-purity graphite standard sample containing blind hole defects with gradient thickness.
[0066] refer to Figure 5-8 , the specific implementation steps are:
[0067] 1. Prepare a high-purity graphite plate with a size of 240mm*135mm*8mm. Blind holes of different depths and sizes are drilled on the graphite plate, and the blind holes are divided into 4 groups (see Figure 5 ), the diameters of each group of blind holes from top to bottom are: 20mm, 15mm, 10mm and 5mm; the depths of each group are: 7.5mm, 7.0mm, 6.5mm, 6.0mm and 5.5mm. Finally, the graphite defect standard sample was obtained.
[0068] 2. Use the X-ray photographic detection technology to detect the standard sample, and obtain the X-ray photographic film of the standard sample.
[0069] 3. Scan the negative film into an electronic picture to obtain its grayscale image (see Image 6 ), the second and third groups of corresponding defect regions are intercepted on the grays...
Embodiment 3
[0074] Example 3: Designing and preparing a two-dimensional stacked C / SiC material standard sample with blind hole defects with varying thickness.
[0075] refer to Figures 9 to 12 , the specific steps are:
[0076] 1. Select two-dimensional laminated carbon cloth as the prefabricated body, and cut it into a thin plate shape with a size of 240mm*135mm*8mm. The pyrolytic carbon interface layer was deposited on the preform, and the process conditions were as follows: deposition temperature: 800°C, pressure 0.2Kpa, propylene flow rate 35ml / min, Ar gas flow rate 250ml / min, and deposition time 60h.
[0077] The silicon carbide substrate was deposited on the two-dimensional laminated carbon cloth deposited with the pyrolytic carbon interface layer. The process conditions were: deposition temperature 800 °C, pressure 4KPa, H 2 Gas flow 150ml / min, Ar gas flow 250ml / min, trichloromethylsilane temperature 35°C, H 2 The molar mass ratio to MTS is 1:12, and the deposition time is 240h...
PUM
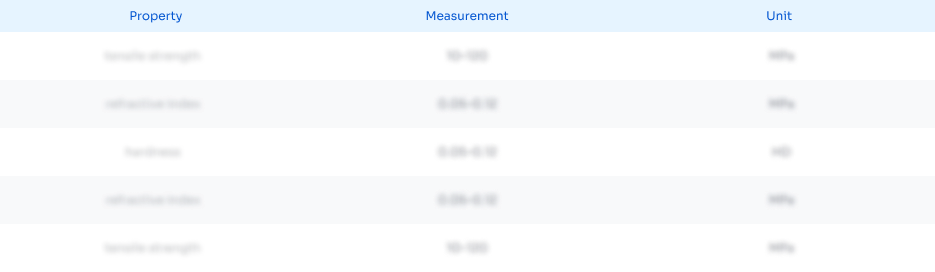
Abstract
Description
Claims
Application Information

- R&D
- Intellectual Property
- Life Sciences
- Materials
- Tech Scout
- Unparalleled Data Quality
- Higher Quality Content
- 60% Fewer Hallucinations
Browse by: Latest US Patents, China's latest patents, Technical Efficacy Thesaurus, Application Domain, Technology Topic, Popular Technical Reports.
© 2025 PatSnap. All rights reserved.Legal|Privacy policy|Modern Slavery Act Transparency Statement|Sitemap|About US| Contact US: help@patsnap.com