Method for preparing solid base catalyst with high specific surface by hybrid composite precursors
A technology of solid base catalyst and hybrid compounding, which is applied in the preparation of organic compounds, catalysts for physical/chemical processes, chemical instruments and methods, etc. It can solve the problems of easy product aggregation, small specific surface area, large sewage discharge, etc., and achieve catalytic High activity, large specific surface area, and narrow pore size distribution
- Summary
- Abstract
- Description
- Claims
- Application Information
AI Technical Summary
Benefits of technology
Problems solved by technology
Method used
Examples
Embodiment 1
[0013] Weigh Mg(NO 3 ) 2 ·6H 2 O and Al (NO 3 ) 3 ·9H 2 O is dissolved in 30ml deionized water to prepare a mixed salt solution, of which Mg 2+ The molar concentration of is 0.3mol / L, Al 3+The molar concentration is 0.1 mol / L; sodium hydroxide and sodium carbonate are used to prepare 30 ml of a mixed alkali solution with a sodium hydroxide molar concentration of 0.64 mol / L and a sodium carbonate concentration of 0.2 mol / L. Pour the prepared mixed salt solution and mixed alkali solution quickly into a colloid mill rotating at high speed (6000 revolutions per minute) at room temperature, and stir vigorously for 5 minutes. Centrifuge the obtained suspension, and then wash it to pH= 7. Obtain a precipitate. Dissolve 0.54g glucose in 30ml deionized water to prepare a solution, and add the resulting precipitate, wherein the molar ratio of metal ions to sugar in the precipitate is 0.25; transfer the above mixed solution to a high-pressure reactor with a polytetrafluoroethylene liner Afte...
Embodiment 2
[0016] Weigh Mg(NO 3 ) 2 ·6H 2 O, Ca(NO 3 ) 2 ·4H 2 O, and Al(NO 3 ) 3 ·9H 2 O is dissolved in 30ml deionized water to prepare a mixed salt solution, of which Mg 2+ The molar concentration of is 0.3mol / L, Ca 2+ The molar concentration of is 0.1mol / L, Al 3+ The molar concentration is 0.2 mol / L; sodium hydroxide and sodium carbonate are used to prepare 30 ml of a mixed alkali solution with a sodium hydroxide molar concentration of 1.0 mol / L and a sodium carbonate concentration of 0.5 mol / L. Pour the prepared mixed salt solution and mixed alkali solution quickly into a colloid mill rotating at high speed (5000 revolutions per minute) at room temperature, vigorously rotate and stir for 2 minutes, centrifuge the obtained suspension, and then wash with water until PH= 7. Obtain a precipitate. Dissolve 3.24g of sucrose in 30ml of deionized water to prepare a solution, and add the resulting precipitate, in which the molar ratio of metal ions to sugar in the precipitate is 1.0; the above m...
Embodiment 3
[0019] Weigh Mg(NO 3 ) 2 ·6H 2 O, Co(NO 3 ) 2 ·6H 2 O, Cu(NO 3 ) 2 ·6H 2 O and Al (NO 3 ) 3 ·9H 2 O is dissolved in 30ml deionized water to prepare a mixed salt solution, of which Mg 2+ The molar concentration is 0.4mol / L, Cu 2+ The molar concentration of is 0.1mol / L, Co 2+ The molar concentration of is 0.05mol / L, Al 3+ The molar concentration is 0.3 mol / L; sodium hydroxide and sodium carbonate are used to prepare 30 ml of a mixed alkali solution with a sodium hydroxide molar concentration of 2.5 mol / L and a sodium carbonate concentration of 1.0 mol / L. Pour the prepared mixed salt solution and mixed alkali solution quickly into a colloid mill rotating at high speed (4000 rpm) at room temperature, vigorously rotate and stir for 3 minutes, centrifuge the obtained suspension, and then wash with water to PH= 7. Obtain a precipitate. Dissolve 3.4g of fructose in 30ml of deionized water to prepare a solution, and add the resulting precipitate, wherein the molar ratio of metal ions to su...
PUM
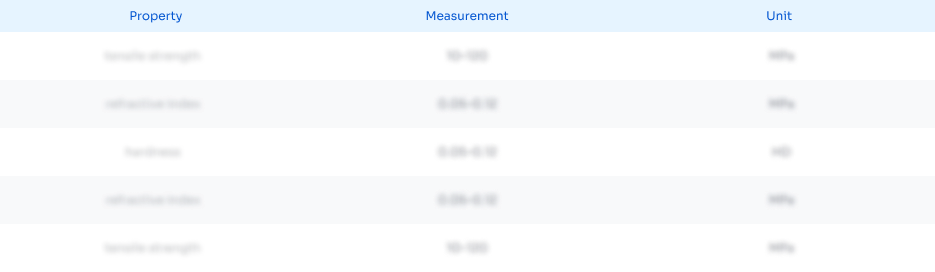
Abstract
Description
Claims
Application Information

- Generate Ideas
- Intellectual Property
- Life Sciences
- Materials
- Tech Scout
- Unparalleled Data Quality
- Higher Quality Content
- 60% Fewer Hallucinations
Browse by: Latest US Patents, China's latest patents, Technical Efficacy Thesaurus, Application Domain, Technology Topic, Popular Technical Reports.
© 2025 PatSnap. All rights reserved.Legal|Privacy policy|Modern Slavery Act Transparency Statement|Sitemap|About US| Contact US: help@patsnap.com