A method for manufacturing recycled wood-plastic composite structural profiles
A composite structure and manufacturing method technology, which is applied in the manufacturing field of recycled wood-plastic composite structural profiles, can solve the problems of the decline of physical and mechanical properties of finished products, good wood fibers are easily carbonized, and the heat resistance of wood fibers is poor. Low cost, reduced viscosity and energy consumption, improved overall quality
- Summary
- Abstract
- Description
- Claims
- Application Information
AI Technical Summary
Problems solved by technology
Method used
Image
Examples
Embodiment 1
[0043] A method for manufacturing recycled wood-plastic composite structural profiles according to the present invention, the formulated mixture formula is as follows:
[0044] Wood chips: 30%
[0045] Polyethylene resin: 40%
[0046] Calcium Carbonate: 10%
[0047] Polyol Parabens: 5%
[0048] Stearic acid: 3%
[0049] Epoxy methyl oleate: 3%
[0050] Lead dibasic stearate: 2.5%
[0051] Polymer paraffin: 1%
[0052] Silane coupling agent: 4%
[0053] Industrial white oil: 1.5%
[0054]Put the mixture prepared according to the above ratio into a grinder to grind the mixture. The particle size of the powder after grinding is 20 meshes. Use a mixer to fully mix the above powder, and then put the powder into the feeding device of the extrusion molding machine; After the mold is installed on the molding machine, the mold and the material pipe are heated. The heating temperature is controlled at 160°C-180°C, and then the discharge valve of the feeding device is opened. The...
Embodiment 2
[0056] A method for manufacturing recycled wood-plastic composite structural profiles according to the present invention, the formulated mixture formula is as follows:
[0057] Crop orange stalks: 40%
[0058] Polyethylene: 20%
[0059] Calcium carbonate: 20%
[0060] Dioctyl phthalate: 4%
[0061] Stearic acid: 2%
[0062] Epoxy methyl oleate: 2%
[0063] Lead dibasic stearate: 3%
[0064] Polyethylene wax: 4%
[0065] Titanate coupling agent: 3%
[0066] Industrial white oil: 2%
[0067] Put the mixture prepared according to the above ratio into a grinder to grind the mixture. The particle size of the powder after grinding is 30 mesh. Mix the above powder thoroughly with a mixer, and then put the powder into the feeding device of the extrusion molding machine; After the mold is installed on the molding machine, the mold and the material pipe are heated. The heating temperature is controlled at 160°C-180°C, and then the discharge valve of the feeding device is opened....
Embodiment 3
[0069] A method for manufacturing recycled wood-plastic composite structural profiles according to the present invention, the formulated mixture formula is as follows:
[0070] Straw: 65%
[0071] PVC: 10%
[0072] Calcium Carbonate: 10%
[0073] Dibutyl phthalate: 3%
[0074] Stearic acid: 1%
[0075] Epoxy ethyl oleate: 1%
[0076] Tribasic lead sulfate: 3%
[0077] Oxidized polyethylene wax: 3%
[0078] Dicumyl peroxide: 3%
[0079] Industrial white oil: 1%
[0080] Put the mixture prepared according to the above ratio into a grinder to grind the mixture. The particle size of the powder after grinding is 50 mesh. The above powder is fully mixed with a mixer, and then the powder is put into the feeding device of the extrusion molding machine; After the mold is installed on the molding machine, the mold and the material pipe are heated. The heating temperature is controlled at 160°C-180°C, and then the discharge valve of the feeding device is opened. The mixture enter...
PUM
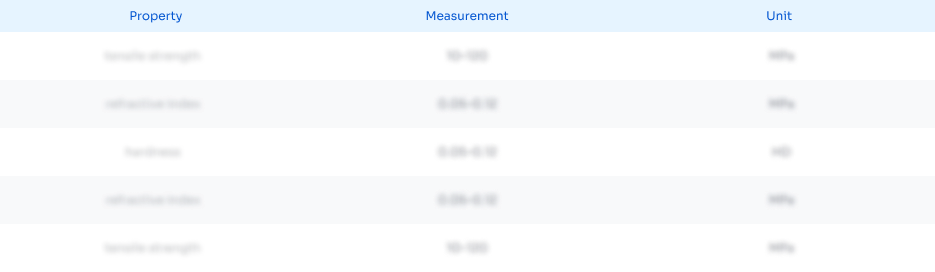
Abstract
Description
Claims
Application Information

- R&D
- Intellectual Property
- Life Sciences
- Materials
- Tech Scout
- Unparalleled Data Quality
- Higher Quality Content
- 60% Fewer Hallucinations
Browse by: Latest US Patents, China's latest patents, Technical Efficacy Thesaurus, Application Domain, Technology Topic, Popular Technical Reports.
© 2025 PatSnap. All rights reserved.Legal|Privacy policy|Modern Slavery Act Transparency Statement|Sitemap|About US| Contact US: help@patsnap.com