Method for improving bagasse alkaline cooking effect through wet process with CEH bleaching waste liquor
A technology of alkaline cooking and bagasse, applied in the direction of digester, pulp bleaching, regeneration of alkali liquor, etc., can solve the problems of loss of pulp yield, industrial development dilemma, waste of resources, etc., to improve clean production and improve pulping. effect, the effect of reducing water consumption per ton of pulp
- Summary
- Abstract
- Description
- Claims
- Application Information
AI Technical Summary
Problems solved by technology
Method used
Examples
Embodiment 1
[0026] Example 1 For the bleaching wastewater of bagasse pulp in section C, section E and section H, the waste water of section E→wastewater of section C→waste water of section H→wastewater of section C→wastewater of section E→wastewater of section C→… so reciprocating and alternately, the piles The bagasse stored in the stockyard is sprayed for 10 minutes every 4 hours, and on the 14th day, it is discharged from the top of the bagasse pile until the pile layer with the original color of fresh bagasse is exposed. The new layer of bagasse continues to be sprayed according to the previous spraying method, and the spraying cycle is still counted by 14 days, so that it is sprayed again and again. The discharged bagasse is sent to the washing machine for 2-3 stages of countercurrent washing. The last stage uses clean water. The liquid after washing and dehydration is sent to the previous washing stage, and the washed and dehydrated bagasse is sent to the cooking equipment. The cond...
Embodiment 2
[0030] Example 2 Repeat Example 1, with the following difference: the bleaching wastewater from Section C, Section E and Section H is mixed in a ratio of 1:1:1 and then the bagasse is sprayed.
[0031] The results of cooking and pulping: the yield of fine pulp is 60~61.5%, the kappa number is 12~13, the whiteness is 37~41%, and the viscosity is 960~1020mL / g.
[0032] Results of bleached pulp: the yield of raw materials is 56-57.5%, the kappa number is 0.8-1.1, the whiteness is greater than or equal to 78%, and the viscosity is 760-810mL / g.
Embodiment 3
[0033] Example 3 Repeat Example 1, with the following difference: the bleaching wastewater from Section C, Section E and Section H is mixed in a ratio of 1:2:2 and then the bagasse is sprayed. The amount of NaOH used for cooking of the processed washed and dehydrated bagasse is 15%, the amount of anthraquinone is 0.1%, and the other conditions are unchanged.
[0034]The results of cooking and pulping: the yield of fine pulp is 60-62%, the kappa number is 12-13, the whiteness is 37-42%, and the viscosity is 980-1030mL / g.
[0035] Results of bleached pulp: the yield of raw materials is 56-58%, the kappa number is 0.7-1.1, the whiteness is greater than or equal to 78%, and the viscosity is 770-810mL / g.
PUM
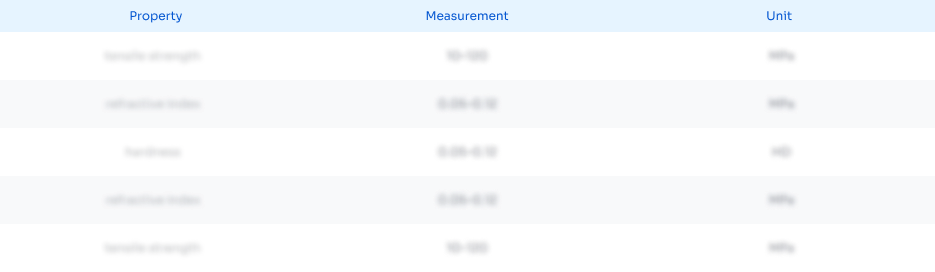
Abstract
Description
Claims
Application Information

- Generate Ideas
- Intellectual Property
- Life Sciences
- Materials
- Tech Scout
- Unparalleled Data Quality
- Higher Quality Content
- 60% Fewer Hallucinations
Browse by: Latest US Patents, China's latest patents, Technical Efficacy Thesaurus, Application Domain, Technology Topic, Popular Technical Reports.
© 2025 PatSnap. All rights reserved.Legal|Privacy policy|Modern Slavery Act Transparency Statement|Sitemap|About US| Contact US: help@patsnap.com