Method for directly separating and purifying cyclopentene from C5 raw material adopting extraction and distillation technology
An extractive distillation and extractive distillation tower technology, which is applied in the field of extractive distillation technology for separating high-purity cyclopentene, can solve the problems of high operation risk and complicated production process, and achieves the advantages of high operation risk and reduced production cost. Effect
- Summary
- Abstract
- Description
- Claims
- Application Information
AI Technical Summary
Problems solved by technology
Method used
Image
Examples
Embodiment 1
[0018] The thermally polymerized C5 raw material enters the first rectification tower in the presence of the polymerization inhibitor tributyl citrate (TBC), and the pressure at the top of the tower is controlled to 0.2Mpa, the reflux ratio is 4, and the temperature is 45°C. Isoprene and low boiling point components are obtained from the top of the rectification tower, and components such as cyclopentene and dicyclopentadiene are obtained from the bottom of the tower. The components in the bottom of the column are sent to the second rectification column, and the pressure at the top of the rectification column is controlled to 0.1 MPa, the reflux ratio is 3, and the temperature is 60°C. Crude cyclopentene is obtained at the top of the tower, and dicyclopentadiene with a purity higher than 99% is obtained at the bottom of the tower. The top component is sent to the extractive distillation column to make it fully contact with the acetonitrile added at the top of the column, the p...
Embodiment 2
[0021] The thermally polymerized C5 raw material enters the first rectification tower in the presence of the polymerization inhibitor TBC, and the pressure at the top of the tower is controlled to 0.25MPa, the reflux ratio is 4, and the temperature is 49°C. Isoprene and low boiling point components are obtained from the top of the tower, and components such as cyclopentene and dicyclopentadiene are obtained from the bottom of the tower. The components in the bottom of the column are sent to the second rectification column, the pressure at the top of the column is controlled to 0.2MPa, the reflux ratio is 3, and the temperature is 68°C. Crude cyclopentene is obtained at the top of the tower, and dicyclopentadiene with a purity higher than 99% is obtained at the bottom of the tower. The top component is sent to the extractive distillation column to make it fully contact with the acetonitrile added at the top of the column, the top pressure of the tower is controlled to 0.35MPa, ...
Embodiment 3
[0024] The thermally polymerized C5 raw material enters the first rectification tower in the presence of the polymerization inhibitor TBC, the pressure at the top of the tower is controlled at 0.4 MPa, the reflux ratio is 3.5, and the temperature is 55°C. Isoprene and low boiling point components are obtained from the top of the tower, and components such as cyclopentene and dicyclopentadiene are obtained from the bottom of the tower. The components in the bottom of the column are sent to the second rectification column, the pressure at the top of the column is controlled to 0.3MPa, the reflux ratio is 4, and the temperature is 72°C. Crude cyclopentene is obtained at the top of the tower, and dicyclopentadiene with a purity higher than 99% is obtained at the bottom of the tower. The top component is sent to the extractive distillation tower to make it fully contact with the acetonitrile added at the top of the tower, and the pressure at the top of the tower is controlled to 0....
PUM
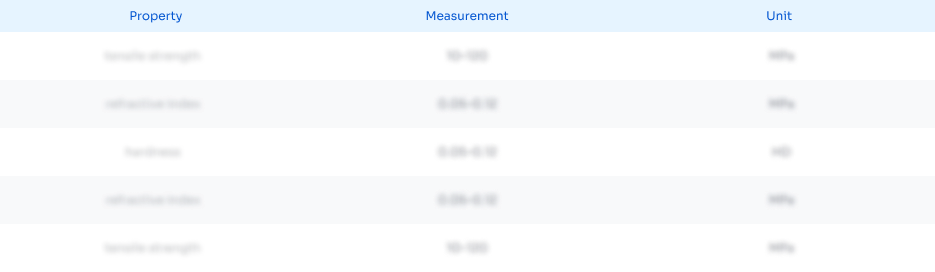
Abstract
Description
Claims
Application Information

- Generate Ideas
- Intellectual Property
- Life Sciences
- Materials
- Tech Scout
- Unparalleled Data Quality
- Higher Quality Content
- 60% Fewer Hallucinations
Browse by: Latest US Patents, China's latest patents, Technical Efficacy Thesaurus, Application Domain, Technology Topic, Popular Technical Reports.
© 2025 PatSnap. All rights reserved.Legal|Privacy policy|Modern Slavery Act Transparency Statement|Sitemap|About US| Contact US: help@patsnap.com