Magnetic rotation conversion straight-moving mechanism
A direct-acting mechanism and magnetic rotation technology, applied in the direction of electromechanical devices, electric components, electromechanical transmission devices, etc., can solve the problems of low efficiency of crank linkage mechanism, complicated manufacturing of crankshaft, misuse of energy, etc., and achieve low cost and long life , high efficiency effect
- Summary
- Abstract
- Description
- Claims
- Application Information
AI Technical Summary
Problems solved by technology
Method used
Image
Examples
Embodiment 1
[0024] Embodiment one: if Figure 1 to Figure 3 Show. The magnetic wheel 1 is composed of a cylindrical permanent magnet 1-2, a cylindrical permanent magnet 1-3, and a non-magnetic cylinder 1-1 fixed on the rotating shaft 1-4. The cylindrical permanent magnet 1-2, the cylindrical permanent magnet 1-3 are all magnetized along the vertical direction, or first arbitrarily determine a plane that passes through the axis of the cylindrical permanent magnet 1-2 or cylindrical permanent magnet 1-3, and make the magnetization direction perpendicular to this plane during magnetization. Looking at the polarity of cylindrical permanent magnet 1-2 and cylindrical permanent magnet 1-3 is opposite (as figure 1 Shown), or cylindrical permanent magnet 1-2, cylindrical permanent magnet 1-3 are respectively spliced by two half cylinders, and magnetization requirement is the same as aforementioned; Rotating shaft 1-4 is installed on frame ( (not drawn) among the figure); Place permanent magne...
Embodiment 3
[0025] Embodiment three: as Figure 5 Show. Two vertically magnetized permanent magnets 7 are placed on the upper and lower sides of the magnetic wheel 6, and the permanent magnets 7 are connected with a linear moving part (not shown) with a coupling.
Embodiment 4
[0026] Embodiment four: as Figure 6 to Figure 8 Show. Magnetic wheel 1 is replaced by magnetic wheel 8, and permanent magnet 2 and permanent magnet 3 are replaced by polarity and permanent magnet 10 above permanent magnet 9. The magnetic wheel 8 consists of several pieces of tile-shaped permanent magnets 8-2 that are alternately magnetized along the radial polarity and several pieces of tile-shaped permanent magnets 8 that are alternately magnetized along the radial polarity that are fixed on the rotating shaft 8-4. -3. Magnetic cylinder 8-5, magnetic cylinder 8-6, and non-magnetic cylinder 8-1. It is required to look at the polarity of the inner and outer arcs of the tile-shaped permanent magnet 8-2 and the tile-shaped permanent magnet along the axial direction. The polarity of the inner and outer arcs of 8-3 is opposite (such as Figure 6 shown), tile-shaped permanent magnets 8-2 and tile-shaped permanent magnets 8-3 are at least two pieces each, or all tile-shaped perman...
PUM
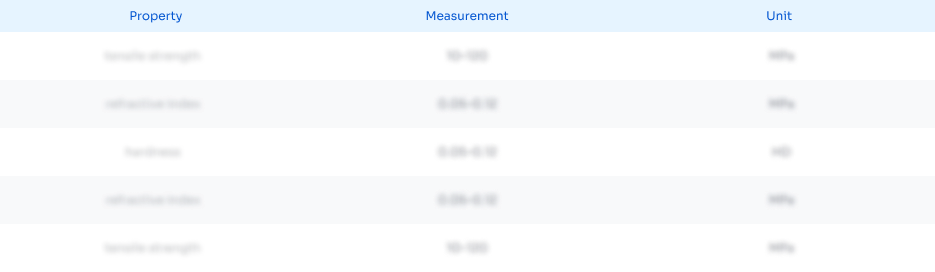
Abstract
Description
Claims
Application Information

- R&D
- Intellectual Property
- Life Sciences
- Materials
- Tech Scout
- Unparalleled Data Quality
- Higher Quality Content
- 60% Fewer Hallucinations
Browse by: Latest US Patents, China's latest patents, Technical Efficacy Thesaurus, Application Domain, Technology Topic, Popular Technical Reports.
© 2025 PatSnap. All rights reserved.Legal|Privacy policy|Modern Slavery Act Transparency Statement|Sitemap|About US| Contact US: help@patsnap.com