Regenerative method of PET wastes
A technology for waste materials and wastes, which is applied in the field of polymer waste recycling, can solve the problems of complex process flow, large alkali-containing wastewater, environmental pollution, etc., and achieves the effect of simple process, environmental protection, and production or purchase cost savings.
- Summary
- Abstract
- Description
- Claims
- Application Information
AI Technical Summary
Problems solved by technology
Method used
Examples
Embodiment 1
[0023] Put 100Kg of waste PET material into the reaction kettle after pulverizing, washing and drying, add 450Kg of ethylene glycol, and then add 100Kg of sodium carbonate after raising the temperature to 180°C, continue to raise the temperature to reflux, keep the steady reflux for 1.5 hours, and then pour it into the reaction kettle Cooling water was passed through to lower the temperature of the system to 120°C, and pressure filtration was carried out at this temperature until the filtration was completed.
[0024] The filter cake is put into a vacuum drier to dry, and the dried filter cake is pulverized and put into an acid analysis kettle, and dissolved with 500Kg boiling water. Then add 30Kg of technical grade sulfuric acid (98%) to precipitate terephthalic acid, centrifuge and dry to obtain refined terephthalic acid (80Kg). Sodium sulfate (80Kg) was recovered by evaporation of the mother liquor obtained by centrifugation.
[0025] The mother liquor after pressure filtr...
Embodiment 2
[0027] Crush, wash and dry 100Kg of waste PET material and put it into the reaction kettle, add 1000Kg of ethylene glycol, heat up to 160°C, then add 150Kg of calcium carbonate, continue to heat up to reflux, keep steady reflux for 2.5 hours, and then cool to 100°C , for pressure filtration.
[0028] The filter cake is put into a vacuum drier for drying. After the dried filter cake is pulverized, it is put into an acid analysis kettle and dissolved with 900Kg boiling water. Then add 60Kg of technical grade sulfuric acid (98%) to separate out terephthalic acid, centrifuge and dry to obtain refined terephthalic acid (78Kg). The mother liquor obtained by centrifugation is evaporated to reclaim calcium sulfate (81Kg).
[0029] The mother liquor after pressure filtration is sent to the distillation still to recover ethylene glycol to obtain ethylene glycol product (28Kg). By-product CO 2 Evacuate through the vent tube.
Embodiment 3
[0031] Put 100Kg of waste PET material into the reaction kettle after pulverizing, washing and drying, add 600Kg of ethylene glycol, heat up to 200°C, then add 100Kg of sodium phosphate, continue to heat up to reflux, keep steady reflux for 2.5 hours, and then cool to 80°C , for pressure filtration.
[0032] The filter cake is put into a vacuum dryer for drying, and the dried filter cake is pulverized and put into an acid analysis kettle, and dissolved with 700Kg boiling water. Then add 120Kg technical grade sulfuric acid (98%) to separate out terephthalic acid, centrifuge and dry to obtain refined terephthalic acid (80Kg). Sodium sulfate (80Kg) was recovered by evaporation of the mother liquor obtained by centrifugation.
[0033] The phosphoric acid ester of ethylene glycol is hydrolyzed to obtain ethylene glycol containing phosphoric acid, and the pure product of ethylene glycol is obtained through distillation to obtain ethylene glycol product (30Kg).
PUM
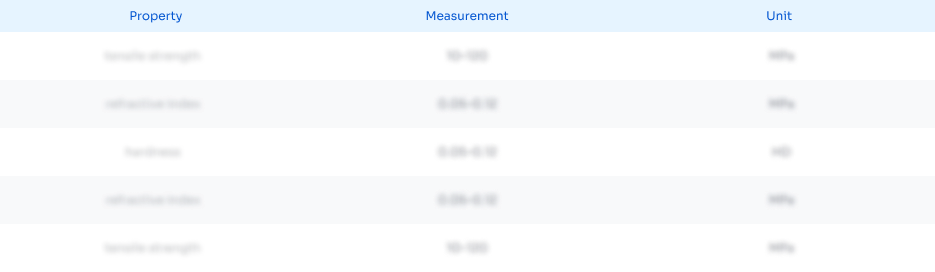
Abstract
Description
Claims
Application Information

- Generate Ideas
- Intellectual Property
- Life Sciences
- Materials
- Tech Scout
- Unparalleled Data Quality
- Higher Quality Content
- 60% Fewer Hallucinations
Browse by: Latest US Patents, China's latest patents, Technical Efficacy Thesaurus, Application Domain, Technology Topic, Popular Technical Reports.
© 2025 PatSnap. All rights reserved.Legal|Privacy policy|Modern Slavery Act Transparency Statement|Sitemap|About US| Contact US: help@patsnap.com