Liquid solid separating method for regenerating filtrate medium in filter
A filter medium and filter technology, applied in the direction of mobile filter element filter, filtration separation, separation method, etc., can solve the problems of increased labor intensity, high labor intensity, long non-working time, etc., and achieve management and maintenance work. The effect of small quantity, convenient replacement and high degree of automation
- Summary
- Abstract
- Description
- Claims
- Application Information
AI Technical Summary
Problems solved by technology
Method used
Image
Examples
Embodiment 1
[0027] Such as figure 1 As shown, it is a schematic diagram of the liquid-solid separation process in which the filter medium is regenerated in the filter. Open the exhaust valve 6, the feed valve 9, the filtrate valve 10, and the slurry valve 13, and close the intake valve 7 and the sewage valve. 11. Filter disc rotation deceleration motor 15, discharge valve 16, flushing valve 17, pump the suspension containing fine solid particles to be separated in the slurry tank 12 into the new quick-opening pressurized leaf filter 4 by the pneumatic diaphragm pump 14 , after the filter 4 is filled with the suspension, close the exhaust valve 6 and continue to send the suspension to the filter for liquid-solid two-phase separation. After the pressure gauge 5 increases to 0.4MPa, close the pneumatic diaphragm pump 14 and the slurry valve 13. Open the intake valve 7 and the discharge valve 16. After the residual suspension in the filter 4 is emptied, close the discharge valve 16. After con...
PUM
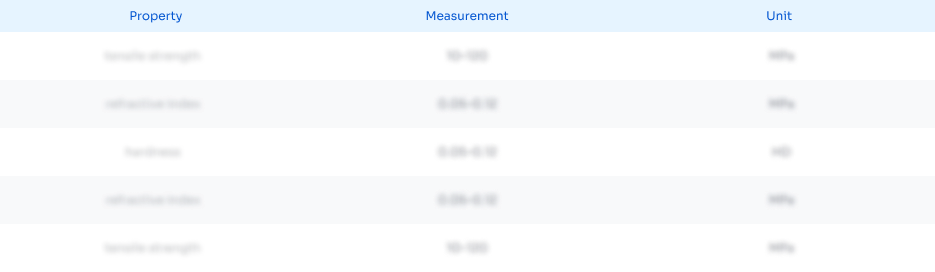
Abstract
Description
Claims
Application Information

- R&D
- Intellectual Property
- Life Sciences
- Materials
- Tech Scout
- Unparalleled Data Quality
- Higher Quality Content
- 60% Fewer Hallucinations
Browse by: Latest US Patents, China's latest patents, Technical Efficacy Thesaurus, Application Domain, Technology Topic, Popular Technical Reports.
© 2025 PatSnap. All rights reserved.Legal|Privacy policy|Modern Slavery Act Transparency Statement|Sitemap|About US| Contact US: help@patsnap.com