Steel box girder assembling construction method
A construction method and technology of steel box girder, which are applied in bridges, bridge construction, erection/assembly of bridges, etc., can solve the problems of large butt joint error of assembly joints, adverse effects on urban traffic and citizens' lives, and difficulty in pier layout, etc. Guaranteed accuracy and quality, simple and easy assembly process, and reduced usage
- Summary
- Abstract
- Description
- Claims
- Application Information
AI Technical Summary
Problems solved by technology
Method used
Image
Examples
Embodiment Construction
[0031] Specific embodiments of the present invention will be described below with reference to the accompanying drawings.
[0032] like Figure 2-5 As shown, the first embodiment includes a temporary pier foundation 1, a column 2, a pier top platform 3, a cantilever steel box girder segment 4, a rear-hanging steel box girder segment 5, a steel box girder top plate splicing joint 6, a bottom plate extension Long stiffener 7, steel box girder web splicing seam 8, U-shaped connecting clip 9, welding support 10, suspension support 11.
[0033] in, figure 1 This is a flow chart of the steps of the preferred embodiment 1 of the steel box girder assembling construction method of the present invention.
[0034] Step 001, the steel box girder is processed and manufactured, the cross section of the segment is according to the design size, and the length direction is set with allowances on the top plate, web plate, and bottom plate; in the processing and manufacturing stage of the stee...
PUM
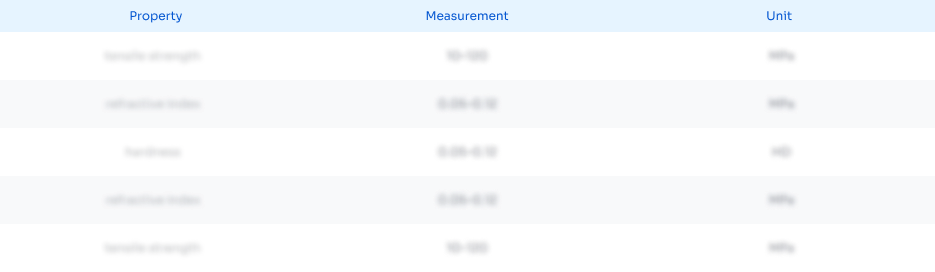
Abstract
Description
Claims
Application Information

- R&D
- Intellectual Property
- Life Sciences
- Materials
- Tech Scout
- Unparalleled Data Quality
- Higher Quality Content
- 60% Fewer Hallucinations
Browse by: Latest US Patents, China's latest patents, Technical Efficacy Thesaurus, Application Domain, Technology Topic, Popular Technical Reports.
© 2025 PatSnap. All rights reserved.Legal|Privacy policy|Modern Slavery Act Transparency Statement|Sitemap|About US| Contact US: help@patsnap.com